Featured Case Studies
Case Studies
Geek+ and George: Optimizing Returns and Fulfillment Processes
The Customer
Founded as part of the larger Asda family, George is a prominent UK-based clothing brand that caters to diverse consumer needs. With its growing online presence and high demand for affordable, high-quality apparel, George faces the continuous challenge of managing extensive inventory and returns, particularly during busy shopping periods such as the holiday season.
The Challenge
George's rapid expansion, coupled with high return volumes and increasing customer expectations, presented several operational challenges:
- Returns Burden: Managing returns during peak seasons strained warehouse operations and delayed getting products back into inventory.
- Fulfillment Efficiency: The need for faster order picking and processing across the warehouse.
- Storage Optimization: Limited storage capabilities made it difficult to manage fluctuating SKU volumes efficiently.
- Labor Demands: Dependence on manual processes increased costs and led to inefficiencies.
Our Solution
To address these challenges, George collaborated with Geek+ and AMH Material Handling to implement an advanced customized goods-to-person returns system, featuring:
- 4-Sided Rack Design: Geek+ deployed its P800 returns solution, which allows workers to perform both picking and put-away tasks simultaneously from any open rack slot.
- Intelligent Automation: The solution automated processes for returning items to inventory, significantly reducing handling time.
- Optimized Storage Locations: By using fewer racks effectively, the solution increased storage location availability while maintaining capacity for 700 SKUs and 7,200 units daily.
- User-Friendly Operations: Designed with worker ergonomics in mind, the system improved ease of use and operational flow for staff.
The Geekplus impact
The implementation delivered measurable results for George, including the following benefits:
- Faster Returns Processing: Returned items were stocked back in inventory on the same day, improving product availability during high-demand periods.
- Higher Fulfillment Rates: Automated picking and put-away capabilities enhanced speed and ensured operational efficiency during peak seasons.
- Optimized Warehouse Utilization: The streamlined storage system allowed George to maximize space and minimize disruptions caused by high stock volumes.
- Enhanced Worker Experience: The ergonomic and intuitive system reduced manual workload, allowing staff to focus on higher-value tasks.
- Improved Customer Satisfaction: Faster order turnarounds ensured timely deliveries, elevating the overall shopping experience.
“I’m delighted to see this project go live, supporting the growth of our George.com business. The collaboration between internal teams, AMH, and Geek+ has resulted in a high-quality solution that enhances the colleague experience and significantly improves operational effectiveness.”
Chris Hall, Vice President, Asda Logistics Services
Video
Geek+ and MedicAir Revolutionize Life-Saving Operations with Robotics
The Customer
MedicAir is a leader in the production and distribution of medical devices and home care support services, dedicated to improving the quality of life for patients. Through its Ventilotherapy unit, MedicAir delivers critical therapies such as oxygen treatment, mechanical ventilation, and artificial nutrition. Its logistics operations are essential to ensuring life-saving supplies reach patients on time, making efficiency and reliability non-negotiable priorities.
The Challenge
MedicAir faced numerous challenges in its logistics operations, which were directly tied to the high stakes of delivering life-saving therapies. These included:
- High-Volume Deliveries: Managing 600 shipments daily for over 100,000 patients required impeccable precision and reliability.
- Demand for Error-Free Operations: Even minor errors or delays could jeopardize lives.
- Operational Inefficiencies: Manual picking processes led to slower workflows and limited scalability in response to peak demand.
- Flexibility Requirements: Seasonal increases in orders and sudden spikes needed immediate adaptability without compromising service levels.
Our Solution
- Fleet of 15 AMRs from Geek+: Advanced AMRs (Autonomous Mobile Robots) model P800 transported shelves directly to operators, reducing unnecessary movement and increasing efficiency; robots were coordinated via Geek+’s Robot Management System (RMS), ensuring seamless operations and optimal route management.
- Shelf-to-Person Model: Instead of requiring workers to travel to retrieve items, shelves are brought to stationary operators at three designated picking stations, streamlining picking and put-away.
- Integrated Warehouse Management: Geek+’s Warehouse Control System (WCS) works in tandem with MedicAir’s Warehouse Management System (WMS), streamlining inventory tracking and fulfillment.
- Collaboration with Industry Experts: Eurofork and Moveo Servizi designed and deployed a fully customized system, aligning robotics and workflow enhancements with MedicAir’s specific operational needs.
The Geekplus impact
The implementation of Geek+ robotics technology delivered exceptional results for MedicAir, including:
- Improved Productivity: Increased picking capacity to handle up to 90 simultaneous orders and 30 ongoing tasks per station.
- Enhanced Efficiency: Productivity soared to processing up to 130 order lines per hour, peaking at 200.
- Error-Free Fulfillment: The shelf-to-person model eliminated manual picking errors, ensuring error-free deliveries critical to patient safety.
- Operational Flexibility: The modular setup allowed rapid scaling by adding AMRs during peak seasons, ensuring uninterrupted service.
- ROI Achieved in Under Three Years: A cost-efficient system with significant long-term savings brought rapid returns on investment for MedicAir.
“From the precision and punctuality of our deliveries depends literally the lives of our patients. The Geek+ solution maximized efficiency, increased flexibility, and improved productivity. It’s a game-changer for MedicAir.”
Elena Pagani, Supply Chain Manager, MedicAir
Geek+ and Dr.Max Streamline E-Commerce Operations with Robotics
The Customer
Dr.Max is a leading pharmaceutical retailer in Romania and Central Europe, managing an extensive portfolio of products ranging from over-the-counter (OTC) medicines to cosmetics and dietary supplements. Its e-commerce operations serve a growing customer base, consistently ranking among Romania’s top 10 websites in terms of unique visitors. With its commitment to quality and innovation, Dr.Max sought to elevate its logistics capabilities to meet surging online demand while ensuring precision in delivering medical goods that directly impact patient well-being.
The Challenge
Dr.Max faced several critical challenges in scaling its e-commerce distribution operations:
- High Order Volume: Managing a diverse inventory of over 25,000 SKUs and processing them efficiently to meet customer expectations.
- Demanding Accuracy Requirements: Achieving near-perfect order fulfillment was vital in delivering essential medical supplies to patients.
- Growth Pressures: Rapidly growing online sales and seasonal peaks necessitated a flexible solution capable of scaling operations seamlessly.
- Waste Management: Minimizing product waste caused by expired inventory further complicated the logistical complexities.
Our Solution
To address these challenges, Geek+ introduced its cutting-edge goods-to-person AMR technology to Dr.Max’s Bucharest warehouse. The solution included:
- Deployment of Nearly 100 AMRs: These robots work tirelessly around the clock, retrieving items from storage and delivering them to picking stations with exceptional efficiency.
- Enhanced Picking System: Geek+ AMRs optimized batch processing, minimizing the need for special orders while considering key factors like expiration dates to reduce inventory waste.
- Scalable Operations: The modular AMR system allows Dr.Max to easily add robots to accommodate seasonal peaks and long-term business growth.
- Advanced Algorithms and Software: Integrated intelligence prioritizes order consolidation, ensuring faster fulfillment while maintaining order accuracy above 99%.
The Geekplus impact
The partnership with Geek+ delivered significant value to Dr.Max’s operations, including:
- Improved Efficiency: The AMRs operate 24/7, ensuring rapid and reliable order processing to keep up with customer demand.
- Enhanced Storage Utilization: Optimized handling of SKUs increased the warehouse’s capacity, accommodating more products without requiring additional space.
- Unmatched Accuracy: Over 99% fulfillment accuracy reduced errors, ensuring timely and precise deliveries to patients.
- Scalability and Flexibility: The ability to expand the AMR fleet provided future-proofing against demand fluctuations.
- Sustainability Improvements: Efficient inventory management reduced product waste, supporting environmental goals.
“Geek+ technology has provided us with a clearer view of our processes and allowed us to meet our patients’ needs more effectively than ever before. Their solutions are a vital part of our logistics strategy as we continue to grow.”
Sorin David, Supply Chain Director, A&D Pharma - Dr.Max Group
Video
Geek+ and Dr.Max Transform Fulfillment with Tote-to-Person Robotics
The Customer
Dr.Max is the largest pharmacy network in Central and Eastern Europe, renowned for its expansive catalog of health and wellness products, including medication, cosmetics, and dietary supplements. With nearly 3,000 outlets and robust e-commerce capabilities, Dr.Max has become a trusted name for consumers seeking reliable and fast access to essential goods. Their new facility in Telgate, Italy is dedicated to e-commerce fulfillment, further extending their ability to deliver products to customers efficiently via home delivery or click-and-collect services.
The Challenge
Operating in a highly competitive and regulated industry, Dr.Max faced a series of escalating challenges:
- Rapid E-Commerce Growth: A 55% increase in online revenue in 2023 placed immense pressure on logistics operations.
- Expanding Product Portfolio: Handling a wide range of goods, including pharmaceutical items and cosmetics, required sophisticated inventory management.
- Faster Delivery Expectations: Meeting customer demands for quick home delivery and pharmacy pickups demanded operational agility.
- Scalability Needs: The growing number of orders required a solution that could adapt to increasing volumes seamlessly.
Our Solution
To address these challenges, Geek+ and SSI Schaefer implemented an advanced Tote-to-Person solution tailored to Dr.Max’s specific requirements. The key components of the solution included:
- 8-Meter-High Shuttle Robot: Facilitating vertical storage and maximizing warehouse space to accommodate a broad product portfolio.
- Fulfillment Robots: Supporting fast and accurate picking of items for efficient order processing.
- Integration with SSI Schaefer Components: Combining robotics with robust logistical infrastructure for a seamless and scalable system.
- Ergonomic Workstations and Intuitive Software: Creating an operator-friendly solution that enhances productivity while reducing physical strain on employees.
- Automated Processes: Including order picking, carton sealing, and shipment preparation for streamlined operations.
The Geekplus impact
The implementation of Geek+ Tote-to-Person technology provided Dr.Max with several measurable benefits:
- Enhanced Efficiency: Automation significantly reduced order processing time, ensuring rapid fulfillment.
- Space Optimization: The vertical storage system improved warehouse capacity without requiring additional physical space.
- Scalability: The flexible system allows for quick adjustments to meet seasonal peaks and growing e-commerce demands.
- Improved Employee Experience: Ergonomic and user-friendly design eased workloads and improved operational accuracy.
- Industry Leadership: The integration positioned Dr.Max as a front-runner in adopting cutting-edge logistics technologies within the pharmaceutical industry.
“Geek+’s mobile robots ensure quick and efficient order processing while providing ergonomic solutions for our employees. This implementation is a game-changer for us as we continue to grow.”
— Miguel Martins da Silva, Group Chief Supply Chain Officer, Dr.Max
Video
Maximizing vertical space for one of the biggest Europe's pharmacy group
The Customer
-
Leading pharmacy chain in Europe with 210+ locations in Italy.
-
Expanded in 2023 with the acquisition of Neo Apotek SpA.
-
Centralized services in 2024 with the 14,000 sqm automated warehouse in Telgate to strengthen omnichannel capabilities and e-commerce.
-
Operates with over 20,000 employees, 3,000 pharmacies, and services across 17 European countries.
The Challenge
- Dr. Max aimed to redefine pharmacies with a clear, distinctive message while serving as a health reference point for local communities.
- Required an efficient solution for order fulfillment in warehouses in their huge network across Czech Republic, Romania, and Italy, including their 14,000 sqm warehouse in Telgate, Bergamo.
Our Solution
- Geek+ implemented Goods-to-Person solutions featuring:
- 8-meter-high RoboShuttle robots for vertical storage.
- P40 Fulfillment robots for fast, accurate picking.
- Manages 11,000+ units for e-commerce and retail.
- Collaboration with SSI Schaefer enabled quick system implementation and integration.The system supports e-commerce and retail deliveries for Italian clients and pharmacies.
The Geekplus impact
Geekplus's flexible, reliable and scalable solutions help Dr. Max to manage market changes with ease and to achieve Business Objectives.
- 3–4x efficiency improvement over manual operations.
- Achieved 99.99% accuracy in order fulfillment.
- Quick implementation completed within 1–3 months.
- Flexible, scalable solutions enable Dr. Max to easily adapt to market changes.
Handling Critical Supply Chain Challenges in the Pharmaceutical industry with Shelf-to-person solutions
About Customer
With over 25 years of experience in the local market, A&D Pharma is one of the largest pharmaceutical groups in Europe, offering pharmaceutical retail and drug distribution services, with a turnover of over 1 billion euros in 2021 and over 5000 employees.
A&D Pharma has two business lines, both of strategic importance: A drug distribution line and a pharmaceutical retail line.
About Partner
One of Europe’s leading chain of pharmacies, Dr.Max, recently upgraded their operations with a fleet of Geek+ shelf-to-person robots. Their distribution center in Bucharest, Romania, is now able to handle over 25 000 items a month with a picking accuracy rate of over 99%. The result is a new experience of shopping for medications for Dr.Max’s patients – the Hyper Pharmacy – where the experience goes beyond simply handing over a prescription and receiving medications.
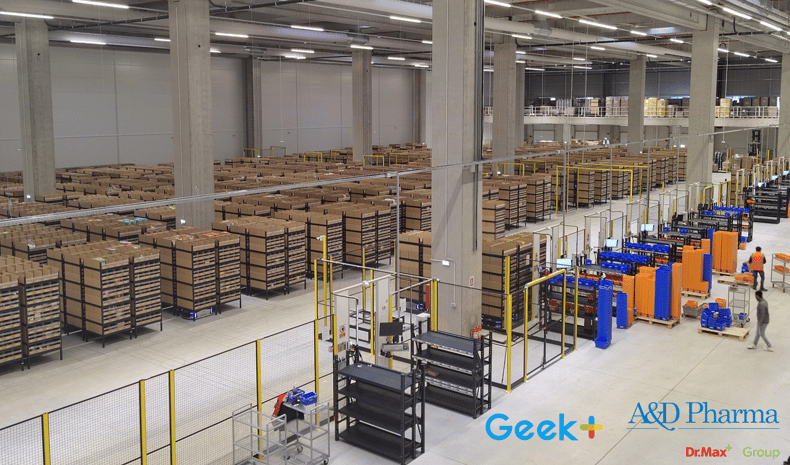
The Challenge
-
The challenge posed by the growth of e-commerce businesses in recent years, as well as the demand of peak season.
-
Delivering products with a very strict best-before date in a faster and more accurate way. Customers need products from outbound operations to be shipped with the correct best-before date (Expiry date)
Our Solution
-
Dr. Max's distribution center in Bucharest (Romania) is operating currently with 96 P500 picking robots. The area in which the Geek+ shelf-to-person solutions operate is 3,200 m2, out of a total warehouse area of 4,830 m2.
-
Dr. Max is able to handle more than 25,000 SKUs per month thanks to Geek+'s warehouse automation. With 99.99% accuracy, Dr. Max is able to handle 180 - 190 lines/hour during peak seasons.
-
Dr. Max has become a gamechanger in the pharmaceutical industry by implementing these solutions. It has become one of the most powerful e-commerce players in Romania and has established a new way of shopping in pharmacies with a concept called Hyper Pharmacies.
The Geek+ impact
-
99.99% accuracy in packet classification
-
The warehouse supports more than 25,000 SKUs per month
-
96 P500 robots working 24/7
-
One of the most important e-commerce platforms in Romania
Pharmaceuticals Company builds supply chain resilience with Tote-to-Person picking
About Customer
Founded in 1999 and headquartered in Wuhan, China, the company is responsible for the distribution of pharmaceutical formulation, TCM and herbs, medical devices, APIs, and more. With a broad domestic distribution network, the company is considered one of China’s leading pharmaceutical companies.
The challenge
- Labor-intensive operations and unsafe work environment
- Strict safety regulations due to COVID-19
- Need for more storage capacity
- Demand for highly accurate operations
Our Solution
- Eight tote-picking RS-2 robots were deployed on a 500 sqm storage area
- Installation of robot compatible shelving, including 3000 totes

The Geek+ impact
- Storage capacity improved by 200%
- Picking efficiency improved by 300%
- Picking accuracy improved by 99.99%
- Improved work environment compatible with current safety regulations
-1.png)
How did Sinopharm Logistics break through its efficiency bottleneck?
Geek+ prioritizes customer-centricity, tailoring its efficient and flexible ‘goods to person’ picking solutions for Sinopharm Logistics.
The customer
Sinopharm Logistics is the logistics arm of Sinopharm, China’s largest pharmaceutical distributor. It is the first third-party professional pharmaceutical logistics company in China, covering warehousing services, drug sales, domestic road freight forwarding and other services.
The challenge
Sinopharm Logistics implements a single drug traceability system to ensure the accuracy of drug shipments, and has a strict multi-vendor, multi-channel and drug quality status management system, which has significantly increased the need for accurate small part picking while increasing overall productivity and lowering labor costs and worker intensity.
Our solution
- Geek+ picking system deployed in 1500sm warehouse, covering 10 workstations and 399 shelving units
- Solution customized for the pharmaceutical industry customized solution such as batch management, quality status management, drug storage compliance management, and expiration date management
- First time use of light selection technology applied to the workstations, so that the individual workstation picking efficiency can be increased to 80-120 lines/hour/person
The Geek+ impact
- Significant picking efficiency increased, from 30-40 lines/hour/person tp 80-120 lines/hour/person
- Manual picking efficiency increased by about 3 times
- Labor intensity greatly reduced
- Ultra-high picking accuracy
How does Jointown Pharmaceutical successfully establish its pharmaceutical logistics innovation model?
Geek+ moving systems help Jointown Pharmaceutical to realize temporary storage automation and unmanned operations of its innovation model.
The customer
Jointown Pharmaceutical Group is the largest private pharmaceutical distribution company in China, distributing international and Chinese drugs and medical equipment. In 2018, the company reported revenues of over $20 billion USD (RMB87 billion yuan) and 1,287 retail points.
The challenge
Jointown Pharmaceutical Group has 127 pharmaceutical logistics centers with a storage capacity of 10 million pieces. Under new requirements the Company set an overall processing volume of 10,000 pieces/hour with 99.9% accuracy.
Our solution
- 100 picking robots deployed and integrated with existing automation, combining with the facility’s conveyor belts and forklifts to provide complete automation over multi-floor temporary storage, involving 1,736 storage space
- Picking robots transport goods directly to the platform for unmanned unloading
- User friendly interface providing multiple data gathering, reducing operation risks and increasing transportation safety
The Geek+ impact
- Saving space: smaller space needed for robot movement and storage capacity increased by 1/3 compared with conventional manual forklift operations
- Significant labor and equipment cost reduction
- ROI under two years
- An innovative model of temporary storage automation and unmanned operations, a blueprint for new pharmaceutical warehouses