Featured Case Studies
Case Studies
Coolshop Transforms Warehouse Operations with Geek+ and Apport Systems
The Customer
Coolshop.com is a Danish-based e-commerce platform that has grown to become a powerhouse in B2B sales as well. With a wide range of product offerings and high service expectations from its customers, Coolshop recognizes the importance of staying ahead with scalable, efficient, and innovative warehouse operations.
The Challenge
Coolshop faced three key challenges in its warehouse operations, driven by its rapid growth and the evolving demands of e-commerce and B2B markets:
- Meeting High Order Volumes: The fast pace of e-commerce required streamlined logistics to manage high order volumes efficiently and accurately.
- Ensuring Precision: With varying customer profiles, order accuracy became critical to maintaining customer satisfaction.
- Reducing Environmental Impact: Coolshop sought to align its operations with sustainable practices, including reducing packaging waste.
Our Solution
Coolshop partnered with Apport Systems and Geek+ to deploy a fully integrated automation solution that addressed its operational challenges. This included a dual focus on robotics and advanced packing technology.
- Geek+ Robotics and Apport WMS:
Geek+ robotics systems, integrated with Apport WMS, streamlined the picking and packing processes for increased speed and precision. The robots efficiently navigated tasks such as item transport and order consolidation, significantly reducing handling times.
- OPERA Packing Machine:
To complement the robotics system, Coolshop implemented the OPERA packing machine, automating the process of product boxing and ensuring optimal packaging for each order. The machine minimized packaging waste by adjusting box sizes to fit orders precisely.
These technologies worked seamlessly together to create a highly cohesive and efficient operation.
The Geekplus impact
The integration of Geek+ robotics, Apport WMS, and the OPERA packing machine delivered impressive results, reshaping Coolshop’s warehouse operations.
- Enhanced Speed and Precision: Optimized workflows enabled faster order fulfillment with near-perfect accuracy.
- Improved Productivity: Productivity soared thanks to automation, with manual labor demands reduced significantly.
- Sustainability Gains: By minimizing packaging waste, Coolshop aligned its warehouse operations with its commitment to environmental responsibility.
- Scalability: The robust integration of these solutions ensured that Coolshop’s operations could scale to meet future growth demands with ease.
“Our partnership with Geek+ and Apport Systems has transformed our warehouse operations. The integration of state-of-the-art robotics and automation technologies, including the OPERA packing machine, has allowed us to achieve unprecedented speed, accuracy, and sustainability in our processes.”
– John Møller, COO, Coolshop.com
THG Fulfil and Geekplus Unite to Create a Peak Season Hero
The Challenge
In the fast-paced world of e-commerce, peak seasons such as Black Friday, Cyber Monday, and the holiday rush present both opportunities and challenges for retailers. Efficient order fulfillment becomes critical to capitalize on increased demand while maintaining customer satisfaction.
Our Solution
Recognizing this, THG Fulfil and Geekplus joined forces to develop a robust solution that would transform peak season operations into a seamless, scalable, and highly efficient process. This collaboration resulted in the creation of a "Peak Season Hero," a comprehensive strategy that leveraged advanced technology and expertise to navigate the complexities of high-volume order fulfillment.
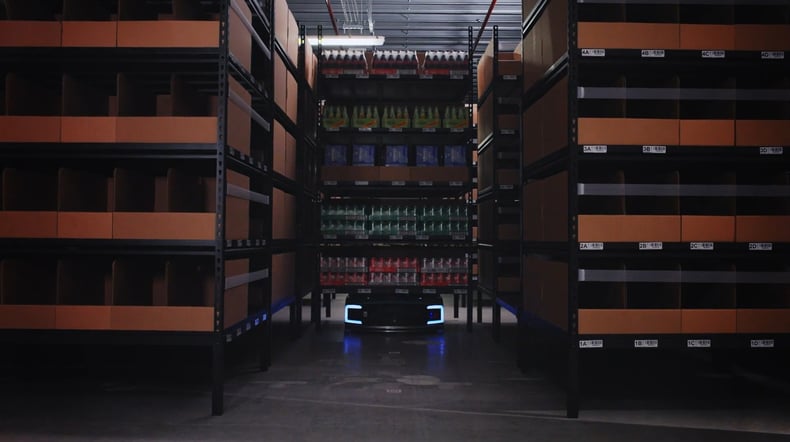
The Geekplus impact
The Geekpus solution joins THG Fulfil’s already extensive warehouse automation solutions, which it leverages to serve the growing trend for late-night shopping by offering a 1 a.m. Next Day Delivery cut-off service for its brands including ESPA and LOOKFANTASTIC, alongside third-party clients.
This innovative order fulfilment solution deployed has helped THG to increase efficiency and enhance customer satisfaction while at the same time enabling scalability and providing real-time data and analytics through an innovative software platform. The expansion of automation solutions now enables THG Fulfil to support category-agnostic items of any size through its automation solutions, pushing 95% of all units sold through a form of automation.
About Partner
THG PLC is a vertically integrated, digital first consumer brands group that operates three distinct businesses in Beauty, Nutrition and Ingenuity, each scaled from the UK to hold global leading positions in their respective sectors.
THG Ingenuity provides cutting-edge ecommerce solutions for clients designed to accelerate brand growth. It comprises THG Commerce, a complete commerce solution with the highest performing technology platform in market THG Fulfil, a provider of world-class fulfilment engineered to improve customer retention, and THG Studios, an award-winning creative agency providing a range of services from campaigns and content creation to videography and photography. With its expertise in building direct to consumer brands, Ingenuity is uniquely positioned to bring pertinent, pragmatic, and global know-how across all aspects of commerce.
THG Fulfil and Geekplus Unite to Create a Peak Season Hero
The Partner
THG PLC is a vertically integrated, digital first consumer brands group that operates three distinct businesses in Beauty, Nutrition and Ingenuity, each scaled from the UK to hold global leading positions in their respective sectors.
THG Ingenuity provides cutting-edge ecommerce solutions for clients designed to accelerate brand growth. It comprises THG Commerce, a complete commerce solution with the highest performing technology platform in market THG Fulfil, a provider of world-class fulfilment engineered to improve customer retention, and THG Studios, an award-winning creative agency providing a range of services from campaigns and content creation to videography and photography. With its expertise in building direct to consumer brands, Ingenuity is uniquely positioned to bring pertinent, pragmatic, and global know-how across all aspects of commerce.
The Challenge
In the fast-paced world of e-commerce, peak seasons such as Black Friday, Cyber Monday, and the holiday rush present both opportunities and challenges for retailers. Efficient order fulfillment becomes critical to capitalize on increased demand while maintaining customer satisfaction.
Our Solution
Recognizing this, THG Fulfil and Geekplus joined forces to develop a robust solution that would transform peak season operations into a seamless, scalable, and highly efficient process. This collaboration resulted in the creation of a "Peak Season Hero," a comprehensive strategy that leveraged advanced technology and expertise to navigate the complexities of high-volume order fulfillment.
The Geekplus impact
The Geekpus solution joins THG Fulfil’s already extensive warehouse automation solutions, which it leverages to serve the growing trend for late-night shopping by offering a 1 a.m. Next Day Delivery cut-off service for its brands including ESPA and LOOKFANTASTIC, alongside third-party clients.
This innovative order fulfilment solution deployed has helped THG to increase efficiency and enhance customer satisfaction while at the same time enabling scalability and providing real-time data and analytics through an innovative software platform. The expansion of automation solutions now enables THG Fulfil to support category-agnostic items of any size through its automation solutions, pushing 95% of all units sold through a form of automation.
Video
Soccer.com and Geek+: Transforming Sports Retail Logistics with Robotics Innovation
The Customer
Soccer.com is a leading online retailer specializing in soccer gear, apparel, and equipment. Catering to players, coaches, and fans, the platform offers a wide range of products, including jerseys, cleats, balls, and training accessories from top global brands. Known for its commitment to the soccer community, Soccer.com also provides customization services, exclusive team gear, and resources to support players at all levels.
Video
Shop LC and Geek+: Transforming E-Commerce Logistics with Smart Automation Solutions
The Customer
Shop LC is a prominent home shopping network and online retailer offering a wide range of affordable luxury products, including jewelry, fashion, beauty, home goods, and lifestyle items. Known for its unique "Low Cost" approach, Shop LC provides exceptional value to customers while supporting sustainability and charitable initiatives through its "Your Purchase Feeds" program, which helps fight hunger globally.
Video
Transforming SP Digital’s Supply Chain with Geek+ and Boreal Automation
The Customer
SP Digital, a leading e-commerce company based in Chile, faced significant challenges managing massive spikes in demand brought on by the COVID-19 pandemic. To tackle these issues, SP Digital partnered with Geek+ and Boreal to implement an advanced robotics solution tailored to optimize their supply chain.
The Challenge
The COVID-19 pandemic drove a surge in online shopping, leaving SP Digital struggling to manage unprecedented demand for computer hardware and gaming products. Their existing supply chain faced inefficiencies in picking processes and warehouse throughput, making it difficult to keep up with the rapid changes in order volumes. To maintain customer satisfaction and sustain business growth, SP Digital sought a robust, efficient, and scalable solution.
Our Solution
Geek+ collaborated with Boreal to deliver a dynamic robotics solution that addressed SP Digital’s challenges. Key components of the implementation included:
- AI-Driven AMRs Geek+ integrated intelligent autonomous mobile robots to automate and optimize the picking processes within SP Digital's warehouses.
- Advanced Picking Robotics Boreal supported the deployment of advanced picking systems, tailored to handle SP Digital’s specific needs.
- Seamless Collaboration Geek+ and Boreal worked closely to ensure a smooth implementation process, minimizing disruptions while maximizing the operational impact.
This combination of smart robotics and collaborative integration resulted in a scalable, efficient, and data-driven warehouse solution.
The Geekplus impact
The deployment of Geek+ AMRs, combined with Boreal's expertise, delivered measurable outcomes:
- Optimized Warehouse Operations Streamlined processes enabled SP Digital to handle rapid shifts in order volumes while maintaining operational stability.
- Maximum Picking Efficiency Robotic automation improved picking speeds, significantly reducing turnaround times and enhancing overall throughput.
- Scalability During Peak Seasons The solution empowered SP Digital to meet massive spikes in demand without compromising accuracy or delivery timelines.
"For us, implementing Geek+ robotics systems in our value chain is an important step towards enriching and strengthening the services we offer our clients. We are very satisfied with the work done together with Boreal and Geek+. The transformation has been remarkable, and we look forward to further collaboration."
Diego Santander, CEO, SP Digital
Video
Rollship and Geek+ Transform E-Commerce Order Fulfillment in Hong Kong
The Customer
Rollship, backed by Chun Sing, has over 20 years of experience managing logistics for the e-commerce sector. Known for its customer-first approach, Rollship specializes in addressing the unique complexities of online retail. Seeking to enhance their operational capabilities, Rollship collaborated with Geek+ to revolutionize their order fulfillment processes in Hong Kong.
The Challenge
- E-Commerce Industry Pressure: Rising demand for faster and more accurate order fulfillment necessitated smarter operations.
- High-Volume Order Management: Handling an increasing number of SKUs demanded a solution to sustain capacity without compromising speed.
- Limited Integration: The need for seamless integration with existing warehouse management systems (WMS) and enterprise resource planning (ERP) platforms.
- Scalability and Seasonal Fluctuations: A logistics partner capable of adapting to changing order volumes and seasonal surges.
Our Solution
Geek+ implemented a range of advanced solutions to address Rollship's challenges:
- PopPick Goods-to-Person Solution: Mobile robotics paired with moveable shelves to enhance picking efficiency, enabling quick fulfillment of orders.
- Four-Way Shuttle System: A high-density storage solution for managing an extensive SKU variety while maximizing warehouse capacity.
- RoboShuttle Tote-to-Person System: Optimized vertical storage and retrieval capabilities, improving throughput and accuracy.
- Seamless Integration: Geek+ software integrated with WMS, ERP, and MES systems, ensuring efficiency without overhauling existing infrastructure.
- Scalability and Flexibility: Systems designed to handle fluctuations in demand, with quick adaptability to seasonal peaks like holidays or major campaigns.
The Geekplus impact
The collaboration resulted in substantial value for Rollship:
- Enhanced Fulfillment Accuracy: Advanced robotics reduced picking errors, ensuring higher customer satisfaction.
- Optimized Space Utilization: High-density storage improved facility use, accommodating more inventory efficiently.
- Significant Efficiency Gain: Automation streamlined operations, boosting order processing speeds and reducing bottlenecks.
- Adaptability for Growth: The scalable system allowed Rollship to confidently expand its operations in line with market demand.
- Integration with Existing Operations: A smooth transition with compatible systems preserved business continuity during
Video
Popick and Moogo Collaboration Accelerates Cold Chain Logistics Efficiency
The Customer
Moogo is a prominent cross-border cold chain company in China. Their state-of-the-art temperature-controlled, automated warehouse occupies over 3,000 square meters in the Ningbo Free Trade Zone. Moogo is dedicated to optimizing storage and distribution while catering to the rigorous demands of e-commerce and supply chain logistics.
The Challenge
-
Inefficient storage systems for managing a high volume of SKUs.
-
Rising pressure from rapid e-commerce development and increased order volumes.
-
High expectations for delivery speed.
-
Complex inventory consisting of multiple product types and sizes requiring enhanced management systems.
Our Solution
Geek+ provided Moogo with the Popick "goods-to-person" picking solution. Key aspects of the solution included:
- Optimized goods-to-person picking powered by advanced robotics.
- Efficient automation to streamline warehouse operations and reduce manual intervention.
- Enhanced inventory management systems ensuring accurate real-time tracking and categorization.
The Geekplus impact
The implementation of Geek+'s solution delivered exceptional results for Moogo:
-
4x Increase in Storage Density — Optimizing the use of space compared to conventional light shelving systems.
-
4x Improvement in Workforce Productivity — Empowering employees with automation to focus on high-value tasks.
-
Enhanced Inventory Management — Modernized systems for efficient tracking and categorization of varied stock.
-
Unmatched Throughput Performance — Meeting the demands of high business volume with ease and reliability.
Video
myEnso and Geek+ Transform Germany's Food Market with Smart Robotics
The Customer
myEnso, founded in 2016, is a trailblazing FMCG platform and online marketplace for food products. With 20,000 SKUs ranging from global brands to local producers, myEnso provides an extensive selection for customers while supporting regional startups and small-scale manufacturers. Committed to reshaping the grocery landscape in Germany, myEnso connects customers with food pioneers and ensures timely delivery of diverse product offerings.
The Challenge
myEnso faced several operational challenges that hindered its growing role in the German food market:
- Increasing Market Demands: Rising consumer reliance on online grocery shopping demanded faster and more accurate order fulfillment.
- Inventory Complexity: Managing 15,000 SKUs while accommodating fluctuating demand was becoming increasingly difficult.
- Labor Shortages: Widespread industry labor challenges made scaling operations and ensuring timely customer service difficult.
- Logistics Bottlenecks: Traditional methods failed to support the flexibility required to handle diverse producer and product types.
Our Solution
To modernize myEnso’s distribution center, Geek+ deployed its goods-to-person robotics solution, which included the following features:
- Autonomous Mobile Robots (AMRs): A fleet of 30 AMRs transported racks of ordered goods from storage zones to workstations, enabling efficient and accurate picking and putaway processes.
- Intelligent Inventory Management: Integrated AI software organized inventory based on real-time demand, ensuring optimal stock levels and faster picking.
- Seamless 24/7 Operations: Robots offered automatic self-charging capabilities to maintain uninterrupted productivity, even during peak periods.
- Scalable System: The solution was designed to accommodate a wide range of producers and product types, fostering inclusivity for small-scale vendors.
- Sustainable Integration: By streamlining operations, myEnso reduced waste and improved resource utilization across its supply chain.
The Geekplus impact
Implementing Geek+ robotics technology resulted in numerous measurable benefits for myEnso:
- Enhanced Efficiency: Automated picking and putaway processes significantly improved both speed and accuracy.
- Flexibility: The system enabled myEnso to handle a wide product mix and address fluctuating demand seamlessly.
- Improved Customer Experience: Faster fulfillment times led to higher customer satisfaction and loyalty.
- Support for Local Producers: By lowering logistical barriers, myEnso empowered smaller vendors to compete effectively in the market.
- Future Growth: The scalable solution positioned myEnso as a leader ready to meet growing online grocery trends.
"When analyzing different solutions, we were impressed with Geek+ long track record of bringing significant improvements to e-commerce players. We look forward to leveraging Geek+ smart robotics systems to improve the efficiency of our online supermarket and better serve our customers with a wider selection of products as well as faster deliveries. By allowing us to flexibly meet fluctuating demand, better handle a wider product mix, and mitigate against widespread labor shortages, it will enable us to, not only adapt and grow, but through better services, drive actual change."
Norbert Hegmann, CEO of Enso e-Commerce GmbH
Video
Geek+ Empowers Webshippy: Transforming E-commerce Fulfillment
The Customer
Webshippy specializes in helping e-commerce companies and online store owners build scalable businesses. The company offers outsourced logistics, dropshipping services, and logistics software solutions for web stores and large enterprises selling online. With a commitment to supporting clients' growth, Webshippy operates as a strategic partner, ensuring efficient and reliable fulfillment services.
The Challenge
Webshippy faced growing challenges due to rapid e-commerce expansion in a competitive market environment.
- Increasing Customer Demands: The rise in e-commerce required faster and more precise parcel delivery to satisfy customer expectations.
- Limited Warehouse Efficiency: Manual processes caused inefficiencies, limiting the workforce's ability to manage order volumes efficiently.
- Space Constraints: Walking paths and inefficient shelf layouts restricted storage capacity, making it challenging to handle increasing inventory needs.
Our Solution
Webshippy partnered with Geek+ to implement an automated goods-to-person solution that directly addressed its operational challenges.
- Robot Deployment: 24 robots were deployed in a 1,500-square-meter warehouse area to automate inventory movement and picking processes.
- Optimized Warehouse Layout: Elevated shelves and cleared walking paths maximized storage density, allowing more inventory to be managed within the same space.
- Employee-Focused Efficiency: Robots handled repetitive and labor-intensive tasks, helping employees focus on value-added activities
The Geekplus impact
The deployment of Geek+ automation technology resulted in these measurable improvements for Webshippy:
- Enhanced Efficiency: Striking a balance between automation and human capabilities, the solution provided employees with an optimal working environment.
- Elimination of Energy-Intensive Tasks: Robots dramatically reduced the time and energy workers spent manually collecting products, accelerating fulfillment processes.
- Maximized Storage Capacity: The restructured warehouse layout and elevated shelves increased overall warehouse capacity, enabling Webshippy to better accommodate rising demand.
Video
How Geek+ and Körber Revolutionized Hawesko's E-commerce Operations
The Customer
Hawesko Group is one of Europe’s largest distributors of premium wine and champagne. With operations in Germany, its facilities handle over 20 million bottles annually. Through its retail, wholesale, and e-commerce divisions, Hawesko maintains its leadership by ensuring exceptional quality and efficient delivery standards for its vast customer base.
The Challenge
Hawesko faced several pressing challenges that threatened its operational efficiency and ability to meet increasing demands in a competitive e-commerce environment:
- Growing E-commerce Demands: Rapid growth in online retail required faster order fulfillment to exceed customer expectations.
- Limited Warehouse Efficiency: Hawesko’s existing manual systems struggled to keep up with increasing order volumes, causing operational bottlenecks.
- Space Restrictions: Expanding warehouses without disrupting current operations was a logistical challenge.
- Scalability: The company needed a solution that could support ongoing growth and seasonal fluctuations in demand.
Our Solution
- Autonomous Mobile Robots (AMRs): 21 robots were deployed to optimize and automate picking operations across a 6,000-square-meter warehouse space.
- Warehouse Expansion and Optimization: The expanded facility included 330 shelves, maximizing storage capacity and accommodating growth.
- Software Integration: Körber's advanced Warehouse Management System (WMS) acted as the central hub, seamlessly coordinating operations. Coupled with Geek+ robots, the Unified Control System (UCS) further enhanced automation and communication efficiency.
- Flexibility and Scalability: The system allowed for the potential addition of up to 100 more shelves in the future, enabling Hawesko to store 40,000 additional items.
The Geekplus impact
The integration of Geek+ automation and Körber’s software solutions delivered impressive results for Hawesko's facility operations:
- 50% Increase in Warehouse Efficiency: Optimized workflows significantly boosted overall productivity.
- Double Picking Performance: Enhanced automation allowed operators to complete order picking faster and with greater precision.
- Improved Space Utilization: Storage area efficiency increased by 30%, facilitating better inventory management.
- Cost-effective Scalability: The solution was cost-efficient and positioned Hawesko for seamless expansion, accommodating seasonal and long-term growth.
"Through our collaboration with Geek+ and Körber, we have revolutionized our warehouse operations, achieving remarkable efficiency and precision. This automation has equipped us to meet e-commerce demands now and into the future, enabling us to provide superior service to our customers."
Frederick Paulsen, Project Manager, IWL Logistics for Hawesko
Video
Boxy and Geek+: Revolutionizing 3PL E-commerce Operations
The Customer
Boxy is a fast-growing 3PL service provider catering to e-commerce businesses in Eastern Central Europe. Known for its innovative approach to logistics, Boxy is dedicated to providing high-quality, flexible, and reliable fulfillment services. With the rapid rise of online shopping, Boxy sought to establish itself as a leader by leveraging state-of-the-art technology to meet the dynamic demands of modern e-commerce.
The Challenge
To maintain its competitive edge and address evolving industry requirements, Boxy faced several key challenges:
- Rising Customer Expectations: Increased consumer demand for faster and more reliable delivery placed pressure on Boxy's fulfillment operations.
- Operational Scalability: Boxy needed a flexible and efficient system to handle fluctuating order volumes, particularly during peak seasons.
- Shipping Performance: Ensuring consistent and timely shipping was critical to maintaining Boxy's reputation and customer satisfaction.
- Efficiency in Labor Utilization: The company aimed to reduce reliance on manual labor and improve workflow ergonomics for its warehouse staff.
Our Solution
To address these challenges, Boxy implemented an advanced logistics solution designed in collaboration with Körber and powered by Geek+'s AMR technology. Key features of the solution included:
- Autonomous Mobile Robots (AMRs): Geek+'s AMRs optimized warehouse operations by automating sorting, picking, and replenishment tasks with unparalleled accuracy and efficiency.
- Integrated Logistics Systems: Körber's end-to-end automation and software solutions provided seamless integration and enhanced operational visibility across Boxy's fulfillment processes.
- Intelligent Workflow Strategies: Real-time AI-driven algorithms enabled efficient inventory placement and retrieval, reducing delays and maximizing throughput.
- Scalable and Flexible Design: The system was built to adapt to Boxy's growth and fluctuating market demands, ensuring future-proof operations.
The Geekplus impact
Boxy experienced significant operational and business enhancements following the implementation of Geek+ solutions:
- Enhanced Efficiency: The deployment of AMRs improved productivity by over 100%, enabling a consistent and efficient flow of goods.
- Improved Shipping Performance: Automation allowed Boxy to meet strict delivery timelines consistently, even during peak demand periods.
- Customer Satisfaction: Faster order processing and timely deliveries secured high customer satisfaction levels and strengthened Boxy's market position.
- Operational Scalability: The flexible system design empowered Boxy to accommodate increasing order volumes seamlessly.
- Employee Productivity and Safety: By automating repetitive tasks, Boxy created a safer and more ergonomic working environment for its employees, allowing them to focus on value-added activities.
“Relying on cutting-edge technology provided by Körber, together with partners like Geek+, has helped us maintain an efficient flow of goods and enhance shipping performance. These automation and software solutions are the future of the industry, driving innovation and giving us a competitive edge.”
András Táncsics, CEO of Boxy
Video