Featured Case Studies
Case Studies
Infios and Geekplus drive efficiency in hardware manufacturing industry at Deutsche Telekom
The Customer
-
One of the world's leading integrated telecommunications companies: more than 261 million mobile customers, 25 million fixed-network lines, and 22 million broadband customers.
-
Deutsche Telekom is present in more than 50 countries. With a staff of some 200,000 employees throughout the world, generated revenue of 115.6 billion Euros in the 2024 financial year.
-
The B2B hardware distribution hub, supplying branches and enterprise customers. It manages 2,200 SKUs with a total stock of 2.5 million units.
The Challenge
- Digitalize B2B hardware logistics to improve efficiency, scalability, and working conditions.
- Reduce unnecessary walking and repetitive manual tasks in inbound and outbound processes.
- Replace outdated logistics technology after only 18 months of planning and development.
Our Solution
As general contractor, Infios deployed an integrated software and robotics solution, centered on the Geekplus Shelf-To-Person P1200 system.
-
- Autonomous Mobile Robots (AMRs) transport shelves of up to 1,200 kg directly to picking and packing stations.
- Manual walking is eliminated, while put-to-light and pick-to-light systems ensure accuracy in order fulfillment.
- Designed throughput: 30 inbound positions per hour and 100 outbound positions per hour, with easy scalability by adding robots or stations.
- All logistics flows are orchestrated by the Infios Unified Control System (UCS), seamlessly integrated into Deutsche Telekom’s IT landscape..
The Geekplus impact
Through Geek+ technology, Infios successfully transformed the Hanover distribution center:
- Operational efficiency: Significant improvement in inbound and outbound speed with minimized human error.
- Workplace ergonomics and safety: Staff relieved from monotonous and physically demanding tasks, improving conditions and reducing risks.
- Scalability and adaptability: Modular and compact solution that can be scaled to meet growing demand with minimal effort.
- Modernization of logistics: Complete replacement of outdated technology with a future-proof, automated system.
Coolshop Transforms Warehouse Operations with Geek+ and Apport Systems
The Customer
Coolshop.com is a Danish-based e-commerce platform that has grown to become a powerhouse in B2B sales as well. With a wide range of product offerings and high service expectations from its customers, Coolshop recognizes the importance of staying ahead with scalable, efficient, and innovative warehouse operations.
The Challenge
Coolshop faced three key challenges in its warehouse operations, driven by its rapid growth and the evolving demands of e-commerce and B2B markets:
- Meeting High Order Volumes: The fast pace of e-commerce required streamlined logistics to manage high order volumes efficiently and accurately.
- Ensuring Precision: With varying customer profiles, order accuracy became critical to maintaining customer satisfaction.
- Reducing Environmental Impact: Coolshop sought to align its operations with sustainable practices, including reducing packaging waste.
Our Solution
Coolshop partnered with Apport Systems and Geek+ to deploy a fully integrated automation solution that addressed its operational challenges. This included a dual focus on robotics and advanced packing technology.
- Geek+ Robotics and Apport WMS:
Geek+ robotics systems, integrated with Apport WMS, streamlined the picking and packing processes for increased speed and precision. The robots efficiently navigated tasks such as item transport and order consolidation, significantly reducing handling times.
- OPERA Packing Machine:
To complement the robotics system, Coolshop implemented the OPERA packing machine, automating the process of product boxing and ensuring optimal packaging for each order. The machine minimized packaging waste by adjusting box sizes to fit orders precisely.
These technologies worked seamlessly together to create a highly cohesive and efficient operation.
The Geekplus impact
The integration of Geek+ robotics, Apport WMS, and the OPERA packing machine delivered impressive results, reshaping Coolshop’s warehouse operations.
- Enhanced Speed and Precision: Optimized workflows enabled faster order fulfillment with near-perfect accuracy.
- Improved Productivity: Productivity soared thanks to automation, with manual labor demands reduced significantly.
- Sustainability Gains: By minimizing packaging waste, Coolshop aligned its warehouse operations with its commitment to environmental responsibility.
- Scalability: The robust integration of these solutions ensured that Coolshop’s operations could scale to meet future growth demands with ease.
“Our partnership with Geek+ and Apport Systems has transformed our warehouse operations. The integration of state-of-the-art robotics and automation technologies, including the OPERA packing machine, has allowed us to achieve unprecedented speed, accuracy, and sustainability in our processes.”
– John Møller, COO, Coolshop.com
Geek+ and K&V Elektro Modernize Distribution with Shelf-to-Person Robotics
The Customer
K&V Elektro is a prominent distributor of electrical installation materials in the Czech Republic. Known for its modern approach to logistics and emphasis on operational efficiency, the company serves a wide range of customers with a constantly expanding product portfolio. To maintain its competitive edge and meet growing customer demands, K&V Elektro sought to modernize its distribution infrastructure with advanced automation.
The Challenge
K&V Elektro needed to address several key challenges to improve its warehouse operations:
- Increase warehouse capacity to store more than 14,000 SKUs.
- Speed up the order picking process to handle up to 7,700 lines/day.
- Automate goods handling operations to reduce reliance on manual labor.
- Improve picking accuracy and operational safety.
- Optimize the use of storage space.
- Seamlessly integrate with the company’s existing SAP ERP system.
These challenges were compounded by a long-term shortage of human resources in the labor market, making automation a critical priority.
Our Solution
Geek+ implemented a Shelf-to-Person robotic warehouse system tailored to K&V Elektro’s needs. The solution included:
-
Racking System:
Shelving racks 2.8 m high with 6 shelves per rack, each capable of holding up to 1,000 kg. The design allowed transport robots to pass under the first shelf for efficient operations. -
25x Geek+ Mobile Robots:
The warehouse was equipped with 25 Geek+ P800 transport AMR robots, which transported racks to inbound and outbound stations. The robots navigated using QR codes on the floor, ensuring precise and efficient movement. -
Inbound Workstations:
Two inbound workstations were used for placing goods on racks. Once goods were confirmed, robots transported the racks to designated storage locations. The receiving capacity was up to 153 items per hour. -
Outbound Workstations:
Three outbound workstations were equipped with Put-to-Wall racks and Pick-to-Light technology. Operators were guided by panels displaying item details, optical pointers, and other tools to ensure accuracy. The system achieved a daily picking performance of 6,020 order lines, with a peak capacity of 7,700 lines/day.
The Geekplus impact
The implementation of Geek+ robotics brought significant improvements to K&V Elektro’s operations:
- Increased Throughput: Enhanced warehouse capacity and daily picking performance, with up to 7,700 lines/day during seasonal peaks.
- Improved Accuracy: Automation minimized errors in goods storage and picking.
- Labor Optimization: Reduced dependency on manual labor, addressing workforce shortages.
- Operational Flexibility: The system easily adapted to fluctuations in demand, such as seasonal peaks.
- Enhanced Transparency: Integration with SAP BW enabled accurate monitoring of performance and deviations.
- Optimized Space Utilization: Efficient use of available warehouse space supported K&V Elektro’s modernization strategy.
Video
Nike fulfills same day delivery in Japan for the first time
Geek+ deployed over 200 robots to help Nike achieve same day delivery.
The Customer
NIKE, Inc. is the world’s leading designer, marketer and distributor of authentic athletic footwear, apparel, equipment and accessories for a wide variety of sports and fitness activities.
The Challenge
With a fast increasing sales of shoes and clothes in Japan, warehouse operators have to walk longer distances back and forth between the storage and packaging areas. Aging population has increased scarcity and the cost of labor.
Our Solution
Geek+ implemented 202 picking robots and 6000 set racks in Nike’s new warehouse, a 10000㎡ area in CHIBA in July 2019.
The Geek+ impact
- Increase picking efficiency
- Mitigate labor shortages
- Streamline warehouse operations to meet the rapid growth in online sales and bring same-day delivery to its Tokyo customers.
- Allowed Nike to expand its e-commerce sales in Japan
Video
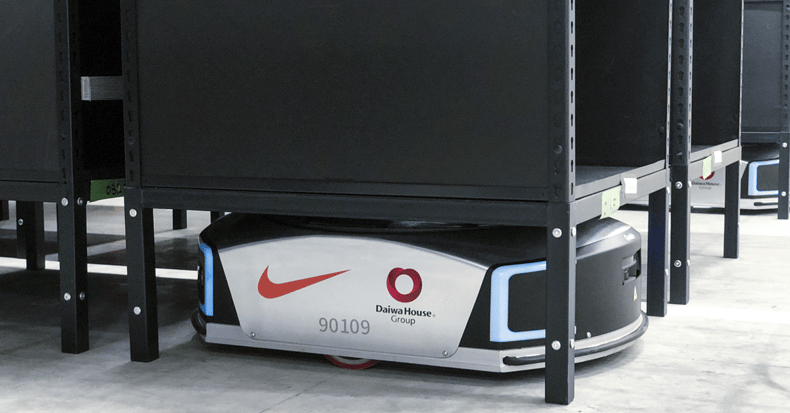
THG Fulfil and Geekplus Unite to Create a Peak Season Hero
The Partner
THG PLC is a vertically integrated, digital first consumer brands group that operates three distinct businesses in Beauty, Nutrition and Ingenuity, each scaled from the UK to hold global leading positions in their respective sectors.
THG Ingenuity provides cutting-edge ecommerce solutions for clients designed to accelerate brand growth. It comprises THG Commerce, a complete commerce solution with the highest performing technology platform in market THG Fulfil, a provider of world-class fulfilment engineered to improve customer retention, and THG Studios, an award-winning creative agency providing a range of services from campaigns and content creation to videography and photography. With its expertise in building direct to consumer brands, Ingenuity is uniquely positioned to bring pertinent, pragmatic, and global know-how across all aspects of commerce.
The Challenge
In the fast-paced world of e-commerce, peak seasons such as Black Friday, Cyber Monday, and the holiday rush present both opportunities and challenges for retailers. Efficient order fulfillment becomes critical to capitalize on increased demand while maintaining customer satisfaction.
Our Solution
Recognizing this, THG Fulfil and Geekplus joined forces to develop a robust solution that would transform peak season operations into a seamless, scalable, and highly efficient process. This collaboration resulted in the creation of a "Peak Season Hero," a comprehensive strategy that leveraged advanced technology and expertise to navigate the complexities of high-volume order fulfillment.
The Geekplus impact
The Geekpus solution joins THG Fulfil’s already extensive warehouse automation solutions, which it leverages to serve the growing trend for late-night shopping by offering a 1 a.m. Next Day Delivery cut-off service for its brands including ESPA and LOOKFANTASTIC, alongside third-party clients.
This innovative order fulfilment solution deployed has helped THG to increase efficiency and enhance customer satisfaction while at the same time enabling scalability and providing real-time data and analytics through an innovative software platform. The expansion of automation solutions now enables THG Fulfil to support category-agnostic items of any size through its automation solutions, pushing 95% of all units sold through a form of automation.
Video
Geek+ and Carrefour Transform Retail Logistics with Robotics Innovation
The Customer
Carrefour, a global leader in the retail industry, operates thousands of stores across over 30 countries, serving millions of customers daily. Renowned for its forward-thinking approach, Carrefour has consistently embraced innovation to enhance every aspect of its operations. By committing to cutting-edge technology in supply chain and logistics, the company continues to revolutionize retail, ensuring seamless, efficient, and customer-centric experiences.
Video
Geek+ and KPI Solutions Help Outdoor Network Boost Efficiency
The Customer
Outdoor Network, a major U.S. distributor of vehicles and OEM parts, faced critical operational challenges, including consolidating multi-line orders across two facilities, labor shortages, and the need to enhance efficiency to meet peak-season demands. Partnering with Geek+ and KPI Solutions, Outdoor Network deployed innovative mobile robotic solutions at their East Coast Distribution Center in Albany, Georgia.
The Challenge
Outdoor Network encountered multiple hurdles in its warehouse operations:
- The need to consolidate multi-line orders from two separate facilities.
- Ongoing labor shortages due to heightened demand for their products.
- A pressing requirement to enhance operational efficiency to cope with peak demands.
These challenges hindered Outdoor Network's ability to maintain high service levels and operational agility, demanding a scalable and efficient solution.
Our Solution
Geek+ and KPI Solutions collaborated to design and implement an advanced automation strategy tailored to Outdoor Network’s needs:
- Integration of Mobile Robotic Solutions: Mobile robots were deployed to handle oversized items, efficiently managing putaway to static shelving and pallet racks.
- Streamlined Picking Operations: Robots transported oversized picks in carts to a dedicated consolidation area for outbound shipping.
- Optimized Single Facility Approach: By merging storage and picking processes into one consolidated facility, operations were simplified and streamlined.
This solution leveraged smart automation to boost storage capacity and efficiency while addressing labor challenges through reduced dependency on manual tasks.
The Geekplus impact
- Increased Efficiency: Streamlined operations with mobile robots reduced order processing time and improved overall workflow.
- Enhanced Storage Capacity: Optimized use of warehouse space by consolidating storage and picking processes into a single facility.
- Labor Optimization: Reduced reliance on manual labor, addressing labor shortages and improving workforce productivity.
- Improved Order Accuracy: Automated processes minimized errors in order picking and consolidation.
- Scalability: The solution provided a flexible and scalable framework to handle peak demands and future growth.
- Cost Savings: Lowered operational costs by reducing manual tasks and improving space utilization.
Video
Geek+ and Körber Help Ariat Transform Supply Chain
The Customer
Ariat International, a leading equestrian and performance footwear and apparel brand, grappled with significant challenges in its supply chain, including labor shortages, pressure to optimize warehouse throughput, and the physical toll on associates. Collaborating with Körber and Geek+, Ariat implemented a cutting-edge robotics solution featuring 88 autonomous mobile robots (AMRs), integration with Körber's K.Motion Warehouse Advantage (WMS), and 2,000 additional racks in their expansive 1 million sq. ft warehouse.
The Challenge
Ariat experienced a surge in customer demand while facing industry-wide labor shortages. Their massive 1 million sq. ft warehouse also posed challenges such as optimizing storage capacity, maximizing throughput, and reducing the physical strain on their warehouse associates due to extensive walking and repetitive manual tasks. To maintain high levels of customer satisfaction, Ariat needed to introduce a scalable and highly efficient solution to transform its supply chain operations.
Our Solution
Geek+ and Körber partnered to implement a cutting-edge robotics solution tailored to Ariat's challenges.
- Robotic Deployment: Geek+ provided 88 AI-driven AMRs designed to automate and streamline picking processes.
- Enhanced Integration: Körber’s K.Motion Warehouse Advantage (WMS) was integrated to ensure seamless interaction between robots, racking systems, and existing warehouse management processes.
- Storage Expansion: 2,000 racks were added to optimize space utilization and enhance throughput within Ariat’s facility.
This solution moved associates away from repetitive manual workloads, allowing them to focus on higher-value tasks while significantly increasing efficiency across the supply chain.
The Geekplus impact
The collaboration between Ariat, Geek+, and Körber yielded impressive results that transformed Ariat’s supply chain operations:
- Improved Efficiency: Warehouse picking efficiency and accuracy experienced significant enhancements, directly impacting speed and reducing errors.
- Associate Productivity Advance: Productivity doubled, with a 100% increase noted following the implementation.
- Reduced Walking Strain on Associates: Associate walking decreased by 82%, minimizing workplace fatigue and improving employee satisfaction.
- Compliance with Demand Surges: The scalability of Geek+’s robots ensured Ariat could effectively meet demand spikes without operational bottlenecks.
"Geek+’s AMRs allow us to move our employees away from repetitive tasks and towards more rewarding activities, resulting in a better working environment and bringing greater value to the services we provide our customers."
Matt Hardenberg, VP of Distribution, Ariat International
Video
GXO and Geek+ Revolutionized Warehouse Operations for a Leading French Sports Retailer
The Customer
GXO is recognized worldwide for its expertise in outsourced logistics and supply chain solutions, delivering tailored strategies to address the dynamic needs of its clients across various industries. This project focused on supporting the logistics network of a leading French sports retailer, a brand renowned for its wide range of products and a heavy reliance on efficient e-commerce order fulfillment.
The Challenge
The French sports retailer faced several operational challenges tied to its growing market demands:
- Rising e-commerce expectations: Increasing consumer demand for rapid order fulfillment highlighted the need for higher picking accuracy and efficiency.
- Storage Constraints: Managing diverse inventory efficiently within the existing warehouse layout was becoming increasingly difficult.
- Seasonal Demand Peaks: Ensuring seamless operations during high-volume periods such as sales promotions and holiday seasons created logistical bottlenecks.
Our Solution
To resolve these challenges, GXO and Geek+ collaborated to deploy an innovative goods-to-person solution powered by 500 autonomous mobile robots in the 12,000-square-meter facility.
- Integrated Robot Systems: The deployment included RS robots, capable of elevating goods to shelves as high as 40 feet to maximize storage density. P40 robots efficiently transported bins along the warehouse floor and delivered them to designated workstations for picking.
- High-Density Storage Design: The warehouse layout was restructured for optimal bin storage, enabling the robots to handle up to 70,000 bins.
- Scalability and Adaptability: The modular design of the automation solution allowed for seamless scaling of operations without interrupting ongoing activities. This structure enabled the warehouse to efficiently handle fluctuating order volumes during seasonal peaks.
The Geekplus impact
The success of this project underscored the strategic value of integrating advanced robotics into warehouse operations:
- Operational Excellence: The streamlined processes improved overall efficiency, allowing GXO to provide superior service to its client.
- Customer Satisfaction:mFaster, error-free order fulfillment bolstered the retailer’s reputation and reinforced trust among its customers.
- Future-Proofing: The scalable and adaptable system positioned the retailer for continued growth and market responsiveness.
“Geek+'s goods-to-person solution has transformed our warehouse operations, significantly enhancing picking efficiency, storage capacity, and adaptability. This deployment underscores our commitment to using advanced robotic technology to address the complexity of global supply chains.”
Rui Marques, General Manager, GXO France
Video
Geek+ and MedicAir Revolutionize Life-Saving Operations with Robotics
The Customer
MedicAir is a leader in the production and distribution of medical devices and home care support services, dedicated to improving the quality of life for patients. Through its Ventilotherapy unit, MedicAir delivers critical therapies such as oxygen treatment, mechanical ventilation, and artificial nutrition. Its logistics operations are essential to ensuring life-saving supplies reach patients on time, making efficiency and reliability non-negotiable priorities.
The Challenge
MedicAir faced numerous challenges in its logistics operations, which were directly tied to the high stakes of delivering life-saving therapies. These included:
- High-Volume Deliveries: Managing 600 shipments daily for over 100,000 patients required impeccable precision and reliability.
- Demand for Error-Free Operations: Even minor errors or delays could jeopardize lives.
- Operational Inefficiencies: Manual picking processes led to slower workflows and limited scalability in response to peak demand.
- Flexibility Requirements: Seasonal increases in orders and sudden spikes needed immediate adaptability without compromising service levels.
Our Solution
- Fleet of 15 AMRs from Geek+: Advanced AMRs (Autonomous Mobile Robots) model P800 transported shelves directly to operators, reducing unnecessary movement and increasing efficiency; robots were coordinated via Geek+’s Robot Management System (RMS), ensuring seamless operations and optimal route management.
- Shelf-to-Person Model: Instead of requiring workers to travel to retrieve items, shelves are brought to stationary operators at three designated picking stations, streamlining picking and put-away.
- Integrated Warehouse Management: Geek+’s Warehouse Control System (WCS) works in tandem with MedicAir’s Warehouse Management System (WMS), streamlining inventory tracking and fulfillment.
- Collaboration with Industry Experts: Eurofork and Moveo Servizi designed and deployed a fully customized system, aligning robotics and workflow enhancements with MedicAir’s specific operational needs.
The Geekplus impact
The implementation of Geek+ robotics technology delivered exceptional results for MedicAir, including:
- Improved Productivity: Increased picking capacity to handle up to 90 simultaneous orders and 30 ongoing tasks per station.
- Enhanced Efficiency: Productivity soared to processing up to 130 order lines per hour, peaking at 200.
- Error-Free Fulfillment: The shelf-to-person model eliminated manual picking errors, ensuring error-free deliveries critical to patient safety.
- Operational Flexibility: The modular setup allowed rapid scaling by adding AMRs during peak seasons, ensuring uninterrupted service.
- ROI Achieved in Under Three Years: A cost-efficient system with significant long-term savings brought rapid returns on investment for MedicAir.
“From the precision and punctuality of our deliveries depends literally the lives of our patients. The Geek+ solution maximized efficiency, increased flexibility, and improved productivity. It’s a game-changer for MedicAir.”
Elena Pagani, Supply Chain Manager, MedicAir
Geek+ and Hunkemöller Redefine Warehouse Efficiency with Robotics on a Mezzanine
The Customer
Hunkemöller is a global leader in the lingerie and retail industry, with an extensive presence across Europe. Known for its stylish products and customer-centric approach, the brand has consistently embraced innovation to improve operations. The Almere warehouse in the Netherlands serves as a critical hub for fulfilling orders efficiently while maintaining the high service standards that Hunkemöller’s customers expect.
The Challenge
To meet the growing demands of e-commerce while managing space limitations, Hunkemöller faced several challenges, including:
- Space Constraints: A need to utilize the full vertical height of their warehouse efficiently.
- Demanding Order Fulfillment: The pressure to streamline and scale operations due to increasing order volumes.
- Maximizing Automation Potential: A requirement for a solution that integrates technology seamlessly while adhering to sustainability goals.
Our Solution
Hunkemöller partnered with Geek+ to implement a forward-thinking warehouse automation system that addressed these challenges head-on:
- Fleet of 160 Geek+ Robots: Equipped with advanced features, these AMRs optimized movement and storage on the mezzanine floor.
- 8.6-Meter-High Mezzanine: The innovative installation leveraged vertical space, proving that AMRs can operate efficiently at impressive heights.
- Order Picking Optimization: Enhanced speed and precision in item retrieval ensured faster and more accurate processing.
- Smart Storage Utilization: The solution prioritized smarter storage organization, reducing wasted space and increasing productivity.
- Sustainable Infrastructure: Built on a sustainable mezzanine floor, provided by Anera B.V., aligning with Hunkemöller’s environmental responsibility goals.
The Geekplus impact
By integrating Geek+’s robotics technology, Hunkemöller realized significant benefits, including:
- Higher Efficiency: Streamlined order picking processes boosted operational speed and accuracy.
- Space Maximization: The automated solution unlocked previously underutilized vertical warehouse space.
- Scalability: The modular system enables adjustments to accommodate seasonal demand increases.
- Customer-Centric Outcomes: Enhanced fulfillment operations ensured better customer satisfaction and loyalty.
- Sustainability: The mezzanine installation underscored Hunkemöller’s commitment to eco-friendly practices.
Video
Geek+ and Dr.Max Streamline E-Commerce Operations with Robotics
The Customer
Dr.Max is a leading pharmaceutical retailer in Romania and Central Europe, managing an extensive portfolio of products ranging from over-the-counter (OTC) medicines to cosmetics and dietary supplements. Its e-commerce operations serve a growing customer base, consistently ranking among Romania’s top 10 websites in terms of unique visitors. With its commitment to quality and innovation, Dr.Max sought to elevate its logistics capabilities to meet surging online demand while ensuring precision in delivering medical goods that directly impact patient well-being.
The Challenge
Dr.Max faced several critical challenges in scaling its e-commerce distribution operations:
- High Order Volume: Managing a diverse inventory of over 25,000 SKUs and processing them efficiently to meet customer expectations.
- Demanding Accuracy Requirements: Achieving near-perfect order fulfillment was vital in delivering essential medical supplies to patients.
- Growth Pressures: Rapidly growing online sales and seasonal peaks necessitated a flexible solution capable of scaling operations seamlessly.
- Waste Management: Minimizing product waste caused by expired inventory further complicated the logistical complexities.
Our Solution
To address these challenges, Geek+ introduced its cutting-edge goods-to-person AMR technology to Dr.Max’s Bucharest warehouse. The solution included:
- Deployment of Nearly 100 AMRs: These robots work tirelessly around the clock, retrieving items from storage and delivering them to picking stations with exceptional efficiency.
- Enhanced Picking System: Geek+ AMRs optimized batch processing, minimizing the need for special orders while considering key factors like expiration dates to reduce inventory waste.
- Scalable Operations: The modular AMR system allows Dr.Max to easily add robots to accommodate seasonal peaks and long-term business growth.
- Advanced Algorithms and Software: Integrated intelligence prioritizes order consolidation, ensuring faster fulfillment while maintaining order accuracy above 99%.
The Geekplus impact
The partnership with Geek+ delivered significant value to Dr.Max’s operations, including:
- Improved Efficiency: The AMRs operate 24/7, ensuring rapid and reliable order processing to keep up with customer demand.
- Enhanced Storage Utilization: Optimized handling of SKUs increased the warehouse’s capacity, accommodating more products without requiring additional space.
- Unmatched Accuracy: Over 99% fulfillment accuracy reduced errors, ensuring timely and precise deliveries to patients.
- Scalability and Flexibility: The ability to expand the AMR fleet provided future-proofing against demand fluctuations.
- Sustainability Improvements: Efficient inventory management reduced product waste, supporting environmental goals.
“Geek+ technology has provided us with a clearer view of our processes and allowed us to meet our patients’ needs more effectively than ever before. Their solutions are a vital part of our logistics strategy as we continue to grow.”
Sorin David, Supply Chain Director, A&D Pharma - Dr.Max Group
Video