Featured Case Studies
Case Studies
Nike fulfills same day delivery in Japan for the first time
Geek+ deployed over 200 robots to help Nike achieve same day delivery.
The Customer
NIKE, Inc. is the world’s leading designer, marketer and distributor of authentic athletic footwear, apparel, equipment and accessories for a wide variety of sports and fitness activities.
The Challenge
With a fast increasing sales of shoes and clothes in Japan, warehouse operators have to walk longer distances back and forth between the storage and packaging areas. Aging population has increased scarcity and the cost of labor.
Our Solution
Geek+ implemented 202 picking robots and 6000 set racks in Nike’s new warehouse, a 10000㎡ area in CHIBA in July 2019.
The Geek+ impact
- Increase picking efficiency
- Mitigate labor shortages
- Streamline warehouse operations to meet the rapid growth in online sales and bring same-day delivery to its Tokyo customers.
- Allowed Nike to expand its e-commerce sales in Japan
Video
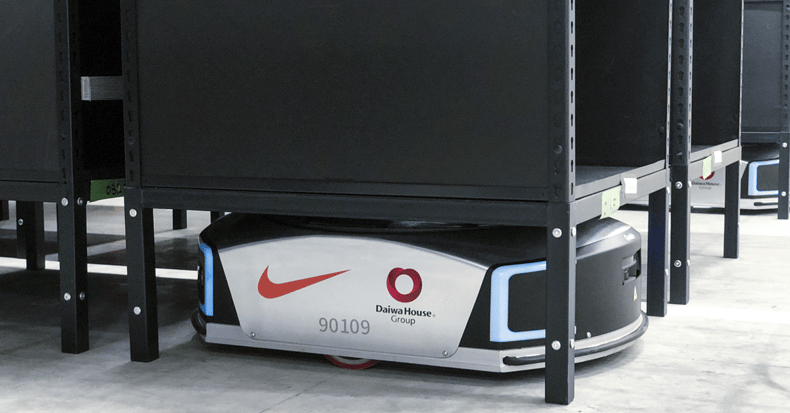
Geek+ and Körber Help Ariat Transform Supply Chain
The Customer
Ariat International, a leading equestrian and performance footwear and apparel brand, grappled with significant challenges in its supply chain, including labor shortages, pressure to optimize warehouse throughput, and the physical toll on associates. Collaborating with Körber and Geek+, Ariat implemented a cutting-edge robotics solution featuring 88 autonomous mobile robots (AMRs), integration with Körber's K.Motion Warehouse Advantage (WMS), and 2,000 additional racks in their expansive 1 million sq. ft warehouse.
The Challenge
Ariat experienced a surge in customer demand while facing industry-wide labor shortages. Their massive 1 million sq. ft warehouse also posed challenges such as optimizing storage capacity, maximizing throughput, and reducing the physical strain on their warehouse associates due to extensive walking and repetitive manual tasks. To maintain high levels of customer satisfaction, Ariat needed to introduce a scalable and highly efficient solution to transform its supply chain operations.
Our Solution
Geek+ and Körber partnered to implement a cutting-edge robotics solution tailored to Ariat's challenges.
- Robotic Deployment: Geek+ provided 88 AI-driven AMRs designed to automate and streamline picking processes.
- Enhanced Integration: Körber’s K.Motion Warehouse Advantage (WMS) was integrated to ensure seamless interaction between robots, racking systems, and existing warehouse management processes.
- Storage Expansion: 2,000 racks were added to optimize space utilization and enhance throughput within Ariat’s facility.
This solution moved associates away from repetitive manual workloads, allowing them to focus on higher-value tasks while significantly increasing efficiency across the supply chain.
The Geekplus impact
The collaboration between Ariat, Geek+, and Körber yielded impressive results that transformed Ariat’s supply chain operations:
- Improved Efficiency: Warehouse picking efficiency and accuracy experienced significant enhancements, directly impacting speed and reducing errors.
- Associate Productivity Advance: Productivity doubled, with a 100% increase noted following the implementation.
- Reduced Walking Strain on Associates: Associate walking decreased by 82%, minimizing workplace fatigue and improving employee satisfaction.
- Compliance with Demand Surges: The scalability of Geek+’s robots ensured Ariat could effectively meet demand spikes without operational bottlenecks.
"Geek+’s AMRs allow us to move our employees away from repetitive tasks and towards more rewarding activities, resulting in a better working environment and bringing greater value to the services we provide our customers."
Matt Hardenberg, VP of Distribution, Ariat International
Video
S&S Activewear: Revolutionizing Apparel Warehousing with the PopPick Solution
The Customer
Founded in 1988 and headquartered in Bolingbrook, Illinois, S&S Activewear is a technology-driven distributor of apparel and accessories, serving the United States and Canada. With a product portfolio spanning over 80 brands, including Adidas and American Apparel, S&S caters to a diverse customer base, including retail brands, e-commerce companies, apparel decorators, promotional product distributors, entertainment merchandise dealers, lifestyle brands, and online custom apparel platforms. The company operates over 4 million square feet of warehouse space across North America, ensuring efficient distribution and delivery.
The Challenge
S&S faced several operational challenges as they scaled their business:
- Optimizing Employee Productivity: Ensuring efficient use of labor resources in a large-scale warehouse environment.
- Improving Order Quality: Maintaining high accuracy in order fulfillment to meet customer expectations.
- Enhancing Delivery Efficiency: Reducing lead times to ensure timely deliveries.
- Addressing Rapid Business Growth: Scaling operations to handle increasing order volumes and customer demands.
Our Solution
To address these challenges, S&S implemented Geek+’s PopPick Goods-to-Person solution. Key features of the solution included:
- Deployment of 340 AMR Robots: These robots automated the movement of goods within the warehouse, reducing manual labor and increasing efficiency.
- 24 PopPick Workstations: These workstations streamlined the picking process, enabling faster and more accurate order fulfillment.
- 2 Inbound/Outbound Workstations: Automated systems for seamless integration with conveyor lines, optimizing inbound and outbound operations.
The Geekplus impact
The implementation of the PopPick solution delivered significant value to S&S’s operations:
- Enhanced Picking Efficiency and Accuracy: The automated system significantly improved the speed and precision of order picking.
- Increased Processing Capacity: The warehouse now processes up to 4,500 order lines per hour, meeting high customer demand.
- Optimized Delivery Speed: Faster order processing and seamless integration with conveyor systems reduced lead times.
- Scalable Operations: The solution provided the flexibility to handle future growth and increased order volumes.
Video
Xtep and Geek+ Enhance Logistics with Smart Warehouse Solutions
The Customer
Xtep Group is an internationally renowned sports shoe and apparel brand with a rapidly expanding footprint, Xtep required a robust logistic solution to keep pace with customer demands and ensure operational agility during fluctuating market conditions.
The Challenge
- Surge in international orders driven by global expansion.
- Seasonal apparel trends necessitating adaptable logistics systems.
- Large SKU varieties requiring advanced storage and inventory solutions.
- Inefficiencies during high-demand periods led to slower picking and bottlenecks.
Our Solution
Geek+ implemented its state-of-the-art RoboShuttle® tote-to-person picking solution tailored to Xtep's requirements:
- Dual-Robot Collaboration: RS robots optimized vertical storage use, while P40 robots facilitated high-speed order picking and delivery.
- Dynamic Picking Operations: Dual picking points at workstations ensured operators could continuously pick without delays.
- Smart Inventory Arrangement: Frequently ordered items were stored on lower, easily accessible racks to accelerate picking speed.
- Flexible Load Management: Compatibility with bins and cartons of all sizes minimized operational costs.
- Scalable and Rapid Deployment: New robots could be seamlessly added during peak periods to meet increased demand.
The Geekplus impact
Xtep's adoption of Geek+'s advanced logistics technology delivered remarkable results:
- 3x Growth in Picking Efficiency: Streamlined workflows and reduced operational delays.
- 5x Increase in Storage Density: Maximizing warehouse space with vertical optimization, saving on rental costs.
- Accelerated Implementation: Quick deployment with minimal disruption to existing operations.
- Cost Savings through Sustainability: Recycling original storage boxes reduced expenses and improved operational processes.
- Future-Proof Scalability: The system's adaptable design ensured readiness for ongoing business growth.
“Xtep is well aware that digital transformation is the key to breaking through development bottlenecks and reshaping the sustainable growth momentum of its business. Therefore, we are committed to promoting the deployment of digital technologies both online and offline. Through our collaboration with Geek+, we have successfully applied logistics robot technology to achieve warehouse transformation in an efficient and low-carbon manner, accelerating the realization of the Five-Five Plan goals and sustainable growth.”
Jun Lin, Assistant Vice President, Xtep
Video
NEXT and Geek+: Transforming Retail Operations with Autonomous Robotics
The Customer
NEXT is a leading UK retailer specializing in clothing, footwear, and home products. With over 700 stores, including 500 in the UK and around 200 across Europe, Asia, and the Middle East, NEXT serves millions of customers annually. A member of the FTSE 100 index, the publicly traded company is recognized for its innovative approach to e-commerce and customer-focused retail solutions.
The Challenge
The fashion industry often experiences dynamic demand cycles and NEXT faced several key operational challenges in keeping up with growing customer expectations:
- Demand Volatility: Customer orders surged unpredictably, creating strain on supply chain operations.
- Manual Process Limitations: Traditional workflows delayed order handling and fulfillment, making it challenging to maintain operational efficiency.
- Delivery Speed Requirements: Rapid same-day and next-day fulfillment became critical during high-demand periods such as sales and promotions.
- Scalability: NEXT required a flexible and future-proof system to efficiently handle growing business demands.
Our Solution
Geek+ deployed a comprehensive robotics solution tailored to NEXT’s operational needs, including the following components:
- Fleet of 250 AMR Robots: The robots enabled seamless automated workflows, managing sorting and picking operations with maximum precision and efficiency.
- Sorting and Picking Automation: Integrated sorting and picking systems streamlined the entire order fulfillment process, from inventory handling to delivery preparation.
- Advanced Robotics Technology: Real-time AI-driven algorithms optimized operations, streamlining inventory placement and retrieval to reduce delays.
- Scalable Design: The system was designed to adapt to NEXT’s evolving needs, allowing for seamless expansion during peak demand or future business growth.
The Geekplus impact
NEXT experienced substantial benefits following the integration of Geek+ AMR robots and automated systems:
- Enhanced Productivity: Warehouse operations saw a 2x boost in efficiency compared to previous manual processes.
- High Order Volumes: NEXT successfully processed over 16,000 products daily, meeting customer demands reliably.
- Same-Day Fulfillment: Automation supported rapid and accurate deliveries, even during peak sales periods.
- Seamless Scalability: The flexible architecture enabled NEXT to manage growing inventory volumes and future-proof its warehouse operations for continued expansion.
Video
Geek+ and George: Optimizing Returns and Fulfillment Processes
The Customer
Founded as part of the larger Asda family, George is a prominent UK-based clothing brand that caters to diverse consumer needs. With its growing online presence and high demand for affordable, high-quality apparel, George faces the continuous challenge of managing extensive inventory and returns, particularly during busy shopping periods such as the holiday season.
The Challenge
George's rapid expansion, coupled with high return volumes and increasing customer expectations, presented several operational challenges:
- Returns Burden: Managing returns during peak seasons strained warehouse operations and delayed getting products back into inventory.
- Fulfillment Efficiency: The need for faster order picking and processing across the warehouse.
- Storage Optimization: Limited storage capabilities made it difficult to manage fluctuating SKU volumes efficiently.
- Labor Demands: Dependence on manual processes increased costs and led to inefficiencies.
Our Solution
To address these challenges, George collaborated with Geek+ and AMH Material Handling to implement an advanced customized goods-to-person returns system, featuring:
- 4-Sided Rack Design: Geek+ deployed its P800 returns solution, which allows workers to perform both picking and put-away tasks simultaneously from any open rack slot.
- Intelligent Automation: The solution automated processes for returning items to inventory, significantly reducing handling time.
- Optimized Storage Locations: By using fewer racks effectively, the solution increased storage location availability while maintaining capacity for 700 SKUs and 7,200 units daily.
- User-Friendly Operations: Designed with worker ergonomics in mind, the system improved ease of use and operational flow for staff.
The Geekplus impact
The implementation delivered measurable results for George, including the following benefits:
- Faster Returns Processing: Returned items were stocked back in inventory on the same day, improving product availability during high-demand periods.
- Higher Fulfillment Rates: Automated picking and put-away capabilities enhanced speed and ensured operational efficiency during peak seasons.
- Optimized Warehouse Utilization: The streamlined storage system allowed George to maximize space and minimize disruptions caused by high stock volumes.
- Enhanced Worker Experience: The ergonomic and intuitive system reduced manual workload, allowing staff to focus on higher-value tasks.
- Improved Customer Satisfaction: Faster order turnarounds ensured timely deliveries, elevating the overall shopping experience.
“I’m delighted to see this project go live, supporting the growth of our George.com business. The collaboration between internal teams, AMH, and Geek+ has resulted in a high-quality solution that enhances the colleague experience and significantly improves operational effectiveness.”
Chris Hall, Vice President, Asda Logistics Services
Video
Geekplus Partners with Körber to Enhance S&S Activewear's Warehouse Operations
The Challenge
With a variety of different SKUs, S&S Activewear needed an automation system that could seamlessly adapt and expand as their business grew.
Our Solution
Geekplus collaborated closely with Körber Supply Chain to optimize warehouse processes at S&S Activewear’s 750,000 sq. ft. facility in Lockport, Illinois. The implementation of Geekplus PopPick robotic solutions enabled S&S Activewear to achieve greater operational speed and throughput. Following the initial deployment, S&S Activewear expanded its partnership with Körber and Geekplus, rolling out Geekplus robotic solutions to three additional warehouse locations across the Americas.
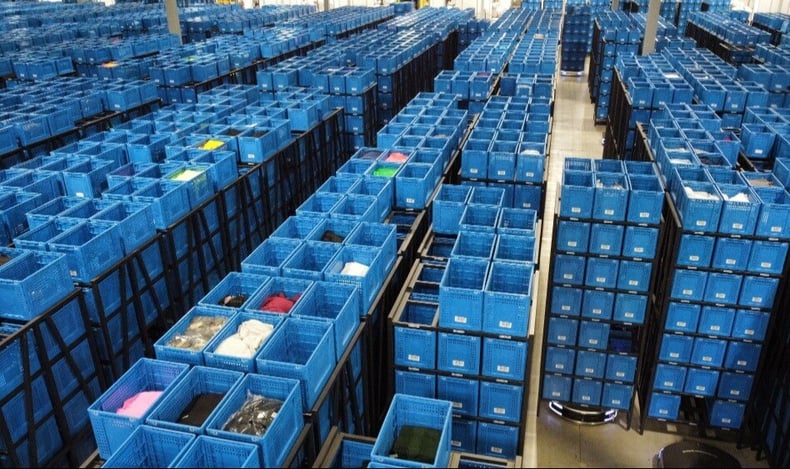
The Geekplus impact
-
Improved picking efficiency, accuracy and throughput
-
S&S Activewear managed up to 16,000 orders daily during peak times
-
Easily scaled to meet the needs of S&S Activewear's growing business
About Customer
Founded in 1988 and headquartered in Bolingbrook, Illinois, S&S Activewear is a the leading technology-enabled distributor of apparel and accessories in the United States and Canada. S&S offers more than 80 brands, including basic garments to fashion-forward styles, with over 4 million square feet of warehouse space across North America. S&S services a broad range of customers through its nationwide network, including retail brands, e-commerce companies, garment decorators, promotional products distributors, entertainment merchandisers, lifestyle brands and web-based platforms for apparel customization.
About Partner
Supply chains are growing more complex by the day. Körber uniquely provides a broad range of proven end-to-end solutions tailored to help manage the supply chain as a competitive advantage. Fitting any business size, strategy or industry, our customers conquer the complexity of the supply chain thanks to our portfolio of software, voice, and robotics solutions – plus the expertise to tie it all together. Conquer supply chain complexity, with Körber. Find out more on www.koerber-supplychain-software.com
Geek+ Equips UPS with Faster E-Commerce Order Fulfillment
About Customer
UPS Supply Chain Solutions® offers a comprehensive portfolio of services to enhance customers' business performance, including logistics, distribution, and transportation.
Allbirds is a global lifestyle brand that innovates with naturally derived materials to make footwear and apparel products in a better way, while tredding lighter on the planet.
The Challenge
With a wide range of order profiles from its footwear and apparel customer, Allbirds, UPS Supply Chain Solutions® needed a scalable yet standardized automation solution that could be seamlessly expanded across multiple distribution centers.
Our Solution
After initially starting with 27 P-800 goods-to-person picking robots, UPS Supply Chain Solutions® scaled its automation to 184 robots across two warehouses covering the West and East Coast of the United States.
The Geek+ impact
- 97% increase in peak unit throughput year over year
- 400% increase in picked units per hour year over year
- Experienced back-to-back record days during Peak
- Multi-lingual system allows for greater employee inclusion
- Accelerated training time from 1 week to approximately 2 hours
- Flexibility to share labor between multiple operations
Geek+ and Körber Digitalize Ariat Supply Chain with Smart Robotics
About Customer
Ariat International, Inc. is a leading manufacturer of innovative performance equestrian footwear, apparel and belts. Featuring a patented technology designed to deliver stability, durability and comfort, Ariat pioneered the application of advanced athletic shoe technology into English riding boots and authentic Western boots, Ariat products are sold in a network of retail outlets throughout the world.
About Partner
Supply Chains are growing more complex by the day. Körber Supply Chain uniquely provides a broad range of proven, end-to-end supply chain solutions fitting any business size, strategy or appetite for growth. Capable of delivering not just software, but automation, voice, robotics, and materials handling - plus the expertise to tie it all together. We are a global partner not just for today, but also as the needs of supply chains continue to evolve.
The Challenge
- Labor Shortages created by the rise in demand
- Needing to optimize the warehouse and increase throughput
- Needing to reduce physical strain for associates
Our Solution
Geek+ worked collaboratively with Körber Supply Chain to optimize throughput and increase storage capacity in Ariat's 1 million sq. ft warehouse operations. Integrating with K. Motion Warehouse Advantage (WMS), 88 Geek+ picking robots and 2,000 racks helped Ariat to achieve greater operational speed and end-customer experience. After its initial order, Ariat expanded the solution with an additional 30 picking robots.
The Geek+ impact
- Improved picking efficiency, accuracy and throughput
- Decreased walking distance by 82% - from 40,000 steps a day to 7,000 steps a day
- Increased associates' productivity by 100%
- Faster and easier training process for associates
- Moral boosting - staff see automation as a way to support them, instead of replacing them
Decathlon Case Study - Europe E-commerce Logistics Upgrade
About Customer
Founded in France in 1976, Decathlon is a professional sports goods retailer specializing in the mass sports market, integrating the entire production chain of sports product design, R&D, production, branding, logistics, and retail. With over 1500 stores in 49 countries, it is the largest sporting goods retailer in the world.
The challenge
New customer expectations for e-commerce – higher volumes of orders and returns, same- and next-day delivery, and nearly perfect accuracy – have brought
new challenges for retailers and a need to address logistics bottlenecks. With 1045 stores in 25 European countries, Decathlon requires a highly flexible and fast supply chain and has turned to Geek+’s goods-to-person solutions to optimize its B2C logistics.
Our Solution
Geek+ tailor-made new robotics solutions for three distribution centers located in Castelnau, France,
Łódź, Poland, and Campania, Italy, use hundreds of P-series picking robots. Unlike traditional infrastructure, the AMR systems allow for flexible maintenance and modification without any interruption of service.
%20Geek+%20a%20transform%C3%A9%20les%20entrep%C3%B4ts%20chez%20D%C3%A9cathlon%20dans%20de%20multiples%20sites%20en%20Europe%20-%20YouTube-1.png?width=640&height=314&name=(2)%20Geek+%20a%20transform%C3%A9%20les%20entrep%C3%B4ts%20chez%20D%C3%A9cathlon%20dans%20de%20multiples%20sites%20en%20Europe%20-%20YouTube-1.png)
The Geek+ impact
-
Expansion of the online customer base across EU
-
Increase storage capacity by up to 30%
-
Increase picking efficiency: 250 order lines per hour per station
-
Increase putaway efficiency: 339 articles per hour per station
-
3x efficiency vs. manual operations
Decathlon Triples Efficiency with Logistics Robots
About Customer
Founded in France in 1976, Decathlon is a professional sports goods retailer specializing in the mass sports market, integrating the entire production chain of sports product design, R&D, production, branding, logistics, and retail. With over 1500 stores in 49 countries, it is the largest sporting goods retailer in the world.
The challenge
The rapid growth of Decathlon's e-commerce business highlighted the limited performance of manual processes. Additionally, as a pioneer of the RFID technology, Decathlon required higher picking efficiency and accuracy to meet its business goals.
Our Solution
- Geek+ provides innovative warehousing solutions for Decathlon’s massive Kunshan warehouse: an RFID technology-based goods-to-person picking and inventory program
- The project area is about 2,000 square meters, with 46 P800 robots, 7 picking stations, and 7 single-point stations. The total inventory of the warehouse is nearly 300,000, involving more than 20,000 SKUs

The Geek+ impact
- Shipment capacity increased to 40,000 pieces/day
- Picking efficiency has reached 300 pieces/hour, 300% increased from manual picking
- Picking system integrated with RFID technology improve inventory management and increase accuracy
- The single-point station adopted to save space and make the operation more flexible

How does Bosideng easily deploy smart logistics?
Geek+ and Bosideng work together to reduce costs and increase efficiency.
The customer
Bosideng, founded in 1976, is the largest manufacturer of down jackets, operating the most advanced production equipment in China, and has over 20,000 employees. Bosideng down jackets are hugely popular in 72 countries, such as the United States, France, Italy, with more than 200 million people wearing them in the world.
The challenge
- In-store sales are growing rapidly, and manual picking has become a bottleneck
- Forklift quantity is overly large, resulting in high costs, and personnel management is difficult;
- Automation rate is low, operation error rate is high
Our solution
- Provide an innovative storage solution for the warehouse operation of the Bosideng warehouse. The seeding container is directly the shipping carton, which is transported to the station through the suspension chain; the seeding wall is of two-layer fluent type, and the back is directly connected with the conveyor line and transported to the packing station for packaging.
- Build a logistics information platform via the logistics information exchange and warning feedback between the functional modules (WMS, WCS, TMS)
- Phase 1 project area covered 5000 square meters, utilizing 116 P800 robots, 15 picking stations and 3 single point stations are deployed. The total design inventory of the whole warehouse is nearly 150000, involving more than 6000 SKUs.
- Phase 2 project area covered 20,000 square meters and utilized 200 sets of P800 robots.
The Geek+ impact
- Delivery capacity increased to 3500 pieces / hour
- Single point RF putaway, reduced site occupation
- Enabled multi batch and small batch store replenishment
- Saved over 10 units of forklifts and over 50 manual workers
- Difficulty of personnel management is reduced, and the operation accuracy is established at 100%