Brilliant PEOPLE Make Brilliant Robots Series: Value Story No.1- Roboshuttle's Evolution
Using AI learning, our robots become 10% smarter each year they work on a warehouse floor. Insanely cool. But who had the idea for this? And WHO built this robot who gets smarter on its own? Brilliant, driven, never-stop-pushing-forward Geek+ employees, that’s who! To celebrate International Workers Day, let’s take a look at the teamwork behind RoboShuttle, the product that defined a new standard in the robot picking industry.
Since its inception in 2016, RoboShuttle production and research teams have trusted and cooperated with each other, launched one new model after another, and implemented one new solution after another, achieving open and win -win results again and again.
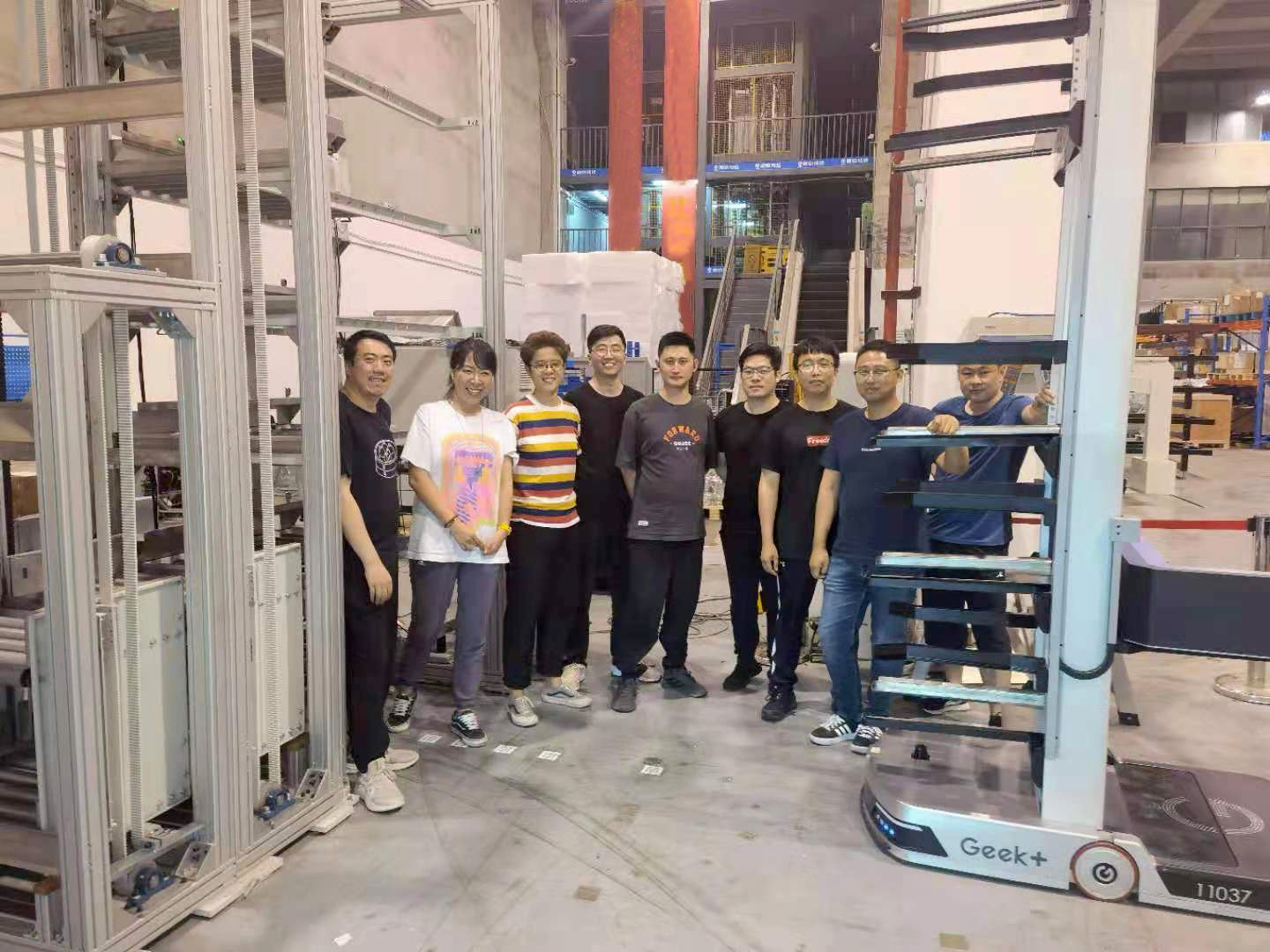
From RS2 to RS5 to RS8, we have seen the robot grow taller and run more stab
ly. From the steel platform to the conveyor line, from the ShuttleDock work station, to the P40, our software, hardware, algorithm, solution and supply-chain teams work together to make solutions from blueprints to reality quickly.
Throughout the creation and deployment of RoboShuttle, every department has experienced daunting challenges.
"The project had a super fast pace, intense cooperation, and tight resources," said an engineer on the project. "There was a lot of hard work and a little arguing, here and there, haha! But everyone had a strong sense of purpose."
The Robot Team spent 1.5 months of round-the-clock work to achieve the rapid launch of the RS5 prototype; the implementation of ShuttleDock work station and when the conveyor line solution required a new layer of system architecture? Our team kicked into high gear.
The function was quickly fixed within a month; from the conception to the implementation of the RS+P40 solution, colleagues from the AI Research Institute (a division of Geek+) led the pre-research simulation, cooperated with Warehouse Management System development, and Risk Management Solutions to optimize functions over and over again.
Just think about the evolution of RoboShuttle. At one point during testing, it dropped boxes repeatedly. After debugging the system together, our colleagues saw that our robot ran more and more steadily and the efficiency climbed. Under the strict delivery time requirements, all materials were delivered smoothly with high quality.
The story comes to this year - 2022. The RoboShuttle production and research team decided to steer the product direction to one that best meets the company's development needs - the fully flexible RS+P40 combination scheme. It is a full-robot solution that can be highly flexible, support high storage, and be highly efficient at the same time. It enables us to achieve market leadership at a lower cost and can achieve fast and convenient delivery and expansion, effectively creating value for customers.
Only teamwork and unrelenting dedication can create and maintain such a technologically advanced product.
Perhaps no one can say it better than one of our engineers: “Our team members were fast to act and quick to respond," he said. "Everyone did their job and never held each other back. Although there were hard times, we all had the same goal. Just get started, and don't stop till you win!"