The Automation Initiatives Under Pandemic
The outbreak of COVID-19 disease has infected more than 100,000 cases globally. WHO has announced COVID-19 disease as a pandemic meaning that it would pose a global spread. Italy has tightened the lockdown policies while the US has just announced restricting travel from Europe. The precautions in these 2 regions are going to be more serious.
In China, although workers are going back to production, most of them are required to quarantine before they get back to work. A Large scale shut down of Chinese manufacturing plants has led to a global supply chain disruption since February. Despite China, other core manufacturing countries like Japan and Korea are now suffering the same outbreak and yet to relieve in a short period. How severe damage does this virus bring to all industries?
A "Death Shot" to all levels in Manufacturing
This accurate lethal shot to manufacturing is unprecedented. It is hard to forecast such disease would bring devastating damage. Here are some factors which are the causes of the"Death shot”:
- Over-reliance of China
China not only exports the raw materials but also abundant of intermediate good or semi-finished goods to other countries for decades. Because of the low cost in labour with good quality, nearly every country purchases the materials and even set up a factory in China. According to a survey by the Institute for Supply Management (ISM) of 628 individuals conducted between February 22 and March 5, almost 75% of U.S. businesses have experienced supply chain disruption as a result of the COVID-19 outbreak. It seems that COVID-19 disease has aroused business owners alert to adopt different supply sources rather than putting all eggs in the same bucket.
- Another Strike From JIT
JIT ”Just-In-Time” is also a vital point for the manufacturing industry especially the global scale factory like Apple and Tesla. To keep a lean and low-cost supply chain, JIT has already adopted widely across most industry.
However, the impeccable lead time is highly demanding for JIT production. This virus disrupted all transportation schedules resulting in a longer delivery time of raw materials. Industries that adopted JIT like automotive and electronics are the first parties getting a direct strike from the virus.
Harsh Production Requirements Under Coronavirus
Labour is by no means the most important factor in the production process. Taking China as an example, assuming workers have their way to get back to work (since lockdown in some cities are still active), they are still required to quarantine for 14 days before normal working. This results in deferring the production schedule and boosting the cost. There are several issues affecting the factories:
- Missing out of specialist in a production line
Some of the production lines required a specialist in a specific procedure for compiling as a final product. If these specialists are missing out, the whole production line would be jammed.
- Keep Good Ventilation and Clean Working environment
If it is needed to continue operation, several strict rules required by the authorities are necessary to be fulfilled before re-opening like good ventilation and a clean environment. This enhances the cost for the business owners.
- Delivery delay after production
Lacking the workers and the border shutdown issue cause the congestion of freight in all transportation. This results in longer delivery time or even manage to deliver.
- Shutdown again if suspicious case reported
Some business owners, especially in China, are not willing to take the risk of re-opening the factory due to the strict punishment if infected workers are reported.
A Cruel “Purge” for All Retailers
Retailers would definitely be the victim. Not mentioning the lack of new stock and supply issues, the sudden economic downturn heavily impacts the consumption market. The global economy is expected to grow by 2.4% in 2020 — down from the 2.9% projected earlier, OECD Economic Outlook Report (March 2020). The post-trade war effects are still yet finished and the virus comes afterward.
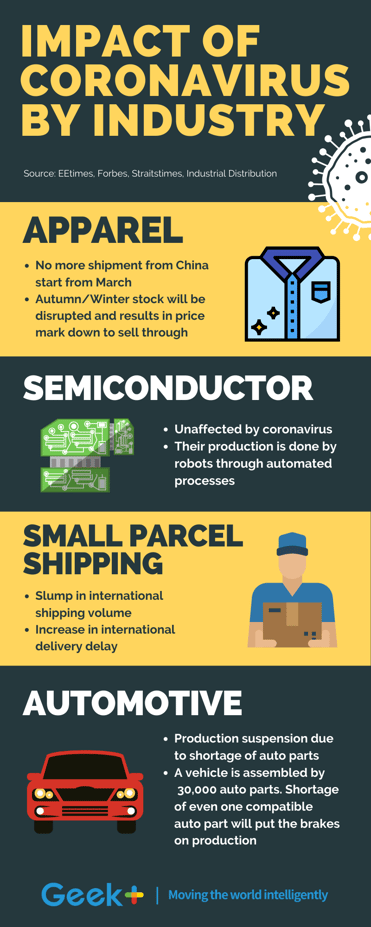
- Late Stock Arrival For Apparel
Take apparel as an example, some apparel retailers have luckily received the last shipment of the stock for spring & summer season before the virus outbreak in China. But after that, the autumn-winter stock will be disrupted or delayed due to worker shortage in the Chinese production plant. If the autumn-winter stock arrives too late, retailers have to mark down the price to sell through which may lead to further revenue reduction after the economic downturn.
- International Shipping Plummet
The small parcel shipping industry is undergoing a slump in international shipping volume and an increase in international delivery delays. Below are how the virus affecting the major carriers:
(Source: Industrial Distribution & Auditshipment.com)
- An Exceptional Industry - Semiconductor
Despite the impact in the above industries, semiconductor production like the chips industry is not largely affected by the coronavirus. It is because their products are mostly done by robots and automation processes. For example, SMIC, TSMC and UMC — have been able to maintain normal production conditions without any changes. In Wuhan itself, semiconductor supplier YMTC has kept its production line running at normal levels. The XMC fab in the Wuhan area is running smoothly as well.
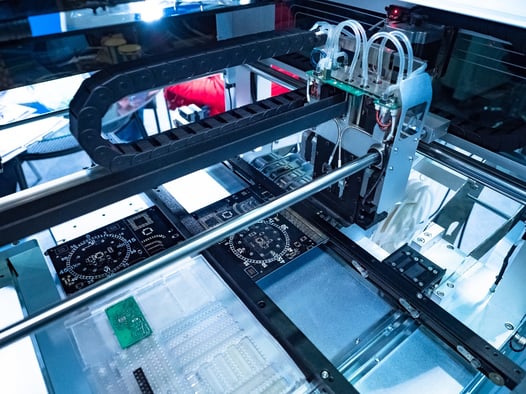
Time to Think About Automation?
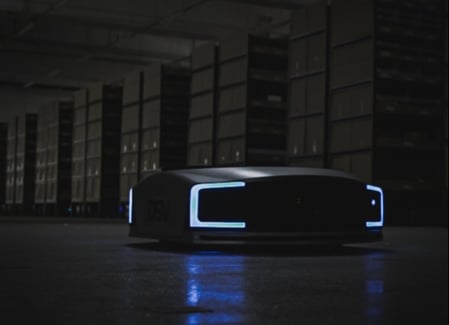
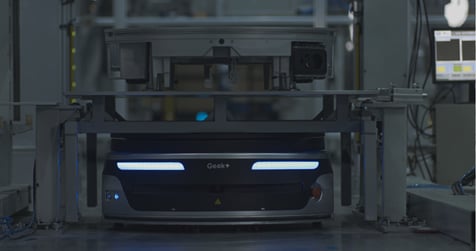
From learning the benefits of automation gained in semi-conductor industry during this pandemic, labour problem could be easily addressed by automation.Therefore, this is under review by other industries to restart the production line or reduce the infection possibility within the manufacturing plants. During current period, with workers staying home and supply chain disrupted, the operation manager has to take automation and industrial robots into consideration so as to prevent the further loss from the shortage of workers and factories closure.
Apart from automation, 6 immediate precautions could be taken.
About Geek+
Geek+ is global technology company leading the intelligent logistics revolution. We apply advanced robotics technologies to realize flexible, reliable and highly-efficient solutions for warehouses, factories and supply chain management.
Our R&D team brings together the brightest robotics, computer science and engineers with industrial engineers that have deep understanding of logistics, enabling us to offer comprehensive solutions to our customers. We develop tailored solutions to a wide range of industries, including e-commerce, apparel, retail, logistics, 3PL, pharmaceutical, and manufacturing.
Geek+ has successfully completed over 200 projects across four continents, deploying more than 10,000 robots. Founded in 2015, Geek+ has over 800 employees and is headquartered in Beijing, with offices in Hong Kong, Japan, Germany and the USA.
About Geekplus
Geekplus is a global leader in mobile robotics technologies. We develop innovative robotics solutions for order fulfilment. More than 770 global industry leaders use our solutions to realize flexible, reliable, and highly efficient automation for warehouses and supply chain management.
Media Contact
Marie Peterson, VP International Marketing & Communications
Marie.peterson@geekplus.com