Geek+ Releases MiniSort, a Brand New Robotic Flexible Sorting Solution
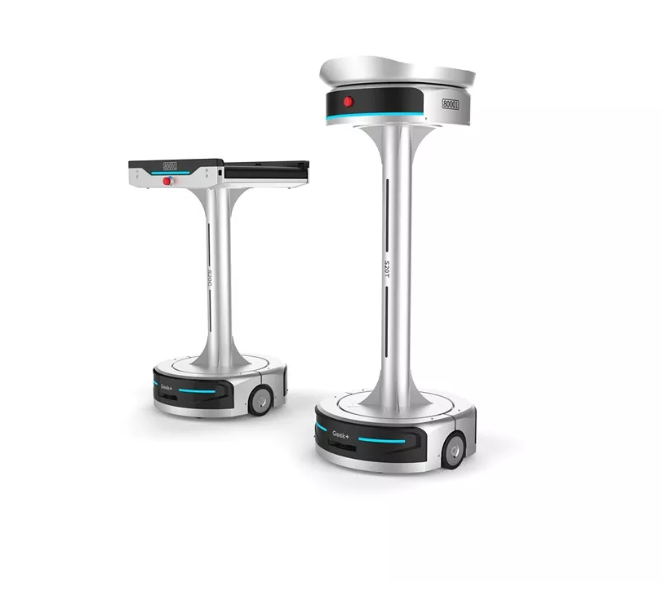
Geek+ Latest S20 Sorting System
[ Industry Background ]
Over the past several decades, warehouse and distribution have been defined as labor-intensive industries. Following the explosive growth of Internet and e-commerce industries, as well as the rapid emergence of new retail, the overall scale of China’s express delivery industry has increased rapidly, with a yearly business volume already surpassing 50 billion items/year. Rapidly changing market requirements have meant that warehouse and distribution industries have had to face many new challenges.
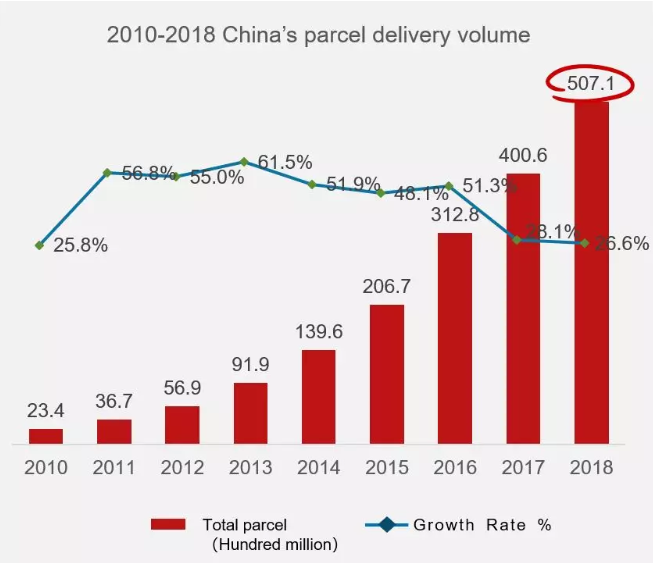
During the sorting stage at the distribution center, there have been greater requirements with regards to adaptability to site dimensions and adaptability to business volume crests and troughs, as well as the flexibility and expandability of staged investments.
As the business volume of the express delivery industry has increased, so too has the need for express mail to have an ever greater sorting efficiency. Automatic cross belt sorters which are used widespread in the industry have a highly efficient processing capacity, but they also have a high cost and are highly inflexible which is a definite cause for concern for many express delivery companies when considering investment. Based on the needs of express delivery and logistics clients for highly efficient and accurate sorting, sorting robot systems have risen to the occasion when they were needed most. MiniSort is the first smart and flexible robotic sorting solution of its kind created by Geek+ and has adapted well to its application in package sorting within the rapidly changing market environment of today. It has effectively reduced labor costs, saved on company expenses, and increased work efficiency.
[ The MiniSort Perspective ]
MiniSort uses the Geek+ S20 line of robots as sorting and transportation devices. Sorting holes can be freely distributed around the edge of the site, and the system is characterized by its high efficiency, reduced labor, and modularization. MiniSort can design a sorting environment based on the actual site requirements of the client, and it is highly adaptable to site locations; No need for fixed platforms and suitable for quick installation. Flexibly expand and adjust sites, destinations, and efficiency based on the crests and troughs of the client's sorting traffic.
Geek+ MiniSort Solution
The S20 series of robots used by MiniSort are highly adaptable when it comes to sorting different sizes and weights of products and are capable of carrying packages up to a maximum size of 600*420*400 mm; The system is highly reliable, and single-unit breakdown does not impact upon the overall operation of the system; 100% sorting accuracy so long as package information is correct, robots are able to automatically pair automated equipment for both incoming and bundled packages. After palletization, Geek+ transport robots or unmanned forklifts can be used to deliver pallets to their corresponding buffer storage or truck areas, allowing for further decreased labor costs.
MiniSort uses a hierarchical design to increase efficiency and use of space. This means that investment costs are far lower than with traditional automated sorting equipment, client labor costs can be reduced by 70%, and returns on investment occur within 2-3 years.
The latest generation of S20 robots from Geek+ use visual-inertial navigation and high-precision laser radar for obstacle avoidance to ensure workplace security to the highest degree possible; Capable of handling various product ranges and able to deliver packages of up to 20 kg in weight; Supports various features including automatic matching with conveyor belts, product fall detection and dynamic delivery. The system is capable of supporting intelligent gathering and deployment of several hundred robots, while at the same time ensuring uninterrupted 24-hour operation of the robotic system.
[ Typical Application Scenarios ]
Replenishing goods, cross-docking and distribution for department store supermarkets:
MiniSort offers a wide range of product-handling capabilities. At package supply terminals belt equipment may be used for automatic pairing, at delivery terminals pairing can be performed with low profile chutes or low profile unpowered roller conveyors allowing for easy handling of various kinds of products or fragile goods up to 20 kg. Rapid and combined pack handling of delivery bags may be selected at receptacles and chutes or roller conveyors may also be used to simplify product buffer storage. The system supports dynamic store adjustment and store quantity may be increased or decreased quickly.
Customer returns and book returns for online retailers:
MiniSort can handle various kinds of customer returns or category-specific returns services with high efficiency and adaptability. It is able to process classification of goods for returns based on SKU, supplier or other pre-defined attributes/categories.
Gathering or separating of orders at the picking stage:
MiniSort supports sorting by order and rapid secondary order separation may be performed after batch orders are collated and picked. Compared with traditional put walls, quantity of orders handled in a single time is increased and efficiency is improved.
Expanded sorting for cross belt sorters:
MiniSort supports both expanded sorting lines and expanded efficiency of traditional cross belt sorters and other such equipment in order to meet a continued increase in business volume with flexible and rapid deployment and a high level of precision.
City and county-level postal depot package sorting:
The MiniSort solution can be used at city and county-level postal depots and other such small and medium-sized package allocation centers to efficiently reduce labor costs and flexibly adapt to the site of the client; Clients can invest in each stage based on their business situation, reducing the financial pressures of fixed investments. MiniSort provides small and medium-sized allocation centers with sorting solutions that are efficient and precise with controllable costs and rapid installation times.
Relay sorting for order picking:
MiniSort is able to match traditional upstream picking systems that pass through multiple pieces of picking equipment or robots, relaying packages to sort them between different target stations, carriers, and zones.
[ Solution Benefits ]
Compared with traditional sorting equipment, MiniSort is a robotic flexible sorting solution. It carries benefits in such areas as system flexibility, convenient expandability, rapid installation, and stage-specific investment; deployment at sorting centers requires basically no fixed installations; and it can achieve a sorting rate of up to 15,000 items/hour.
In the image above, the area within the orange line is the expansion zone
Compact staff role allocation and an average increase in efficiency per worker with the MiniSort solution mean that, for the same processing efficiency, nearly 70% of manual labor costs can be saved for the client compared with a cross belt sorting system, resolving problems relating to aggressive sorting in the express delivery industry and properly ensuring package safety. The S20 robots employ static unloading, so as long as the information written on the front of the package is accurate, the theoretical error ratio for sorting is 0, helping to avoid sorting mistakes from traditional human sorting operations, gaps in sorting, and other such events, further increasing the reliability and accuracy of the logistical services of the client.
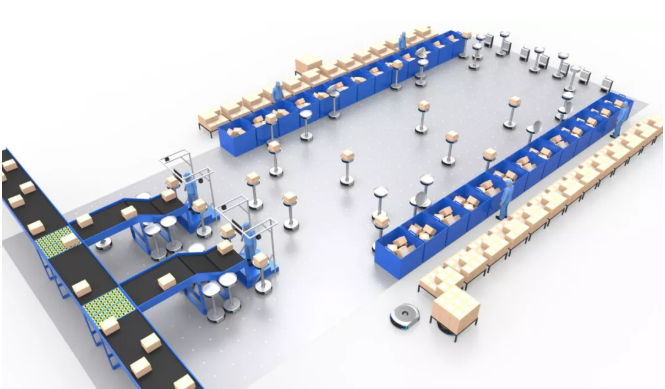
MiniSort operates through a combination of numerous individual S20 robots working together. Their side-by-side processing ability is strong, and the system has no single point of failure, improving the sturdiness of the system. Furthermore, The MiniSort robotic sorting system has a lower power consumption compared with cross belt sorters of the same scale. The robots also employ rapid charging technology and have a high utility. This further reduces equipment operating costs for the client.
[ Solution Expansion ]
Geek+ FleetSort, a Fully Flexible Sorting Solution
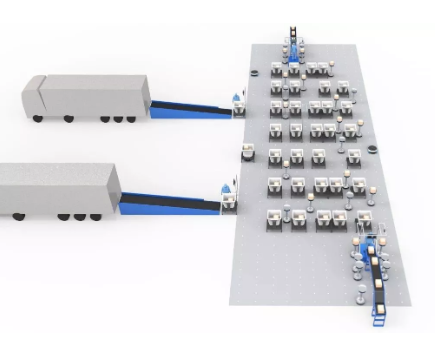
Packages use the Geek+P series of robots for automatic delivery both into and out of the warehouse
FleetSort is another new solution model created by Geek+. Matrix distribution of cage trolleys mean a high level of integration with the sorting area, maximizing destination quantity and reducing sorting area size. FleetSort supports combined operation of both S20 and P-series robots in the sorting areas, with the P-series robots used to complete transport operations. This solution allows for both high-efficiency automatic sorting and intelligent transportation of combined packages. Transportation robots match the locations of packaging and combined packing points in order to adjust dynamically. The site does not require any fixed steel platforms and costs for fixed installations can be reduced as much as possible in order to accomplish rapid and flexible deployment.
FleetSort is especially used for small and medium-sized packages or order-sorting environments with high requirements with regards to efficiency or shelf quantity. It can be flexibly deployed and expanded by module in accordance with the client’s needs and supports rapid unmanned sorting from the unloading to the loading stage.